Coated Diamond Powder
Engineered Coated Diamond Powder for Enhanced Bonding and Tool Life
Improve Grinding Stability with Coated Diamond Powder
Coated diamond powder is designed to improve bond retention, thermal stability, and overall grinding efficiency. Crownkyn’s coated diamond features a uniform metal or ceramic coating (such as Ni, Ti, Cu, Cr, W, Co), enhancing the interface between the diamond and the bond system, especially in resin, metal, and vitrified bond tools.
Produced with strict control over coating thickness and coverage uniformity, our coating diamond powder ensures stable performance and extended tool life in demanding grinding and cutting applications. Choose Crownkyn for coated abrasive solutions that deliver enhanced durability and processing efficiency.
We can provide customized plating of metals such as aluminum (AI), molybdenum (Mo), zirconium (Zr), silicon (Si), copper-tin alloy (CuSn), and copper-chromium alloy (CuCr) on diamond surfaces according to customer requirements.
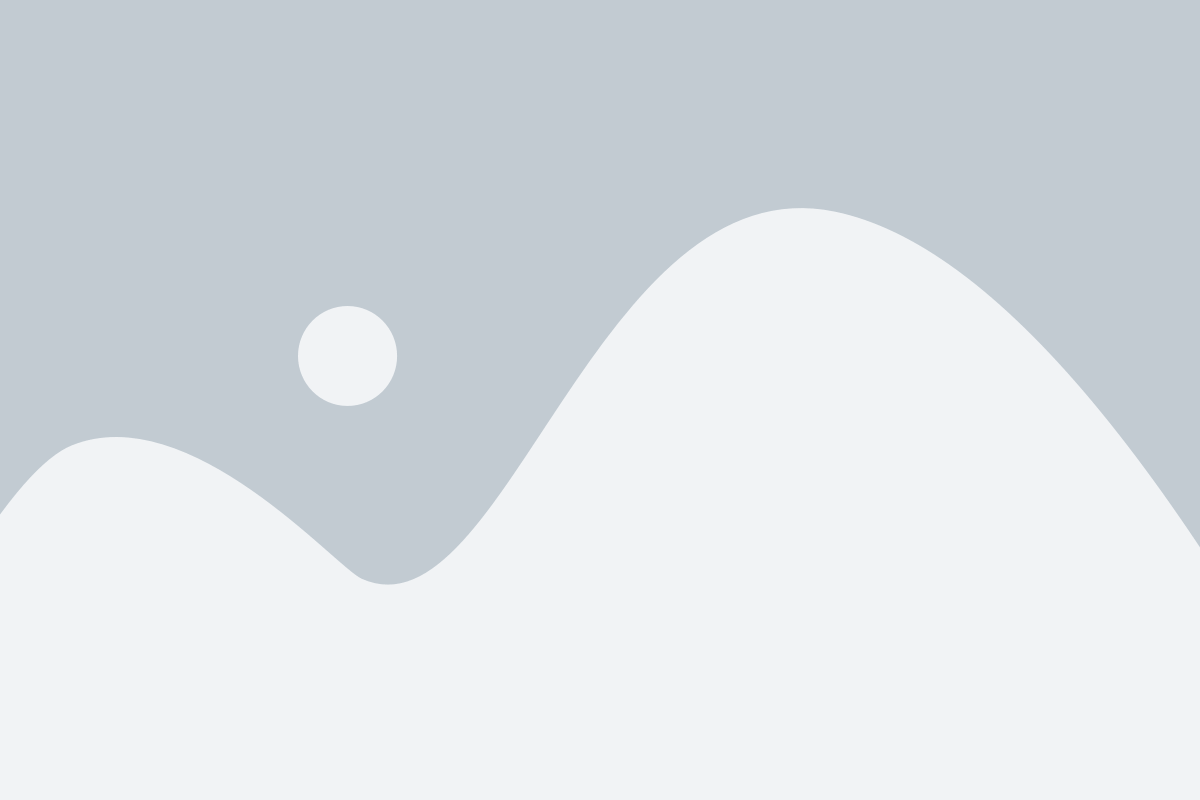
Ti Coated Diamond Powder
Characteristic: Titanium coating diamond powder provides excellent oxidation resistance and improves thermal stability. It enhances bond retention and increases diamond protrusion by improving wettability. The coating does not degrade the diamond surface or strength. Titanium content ranges from 1 wt% to 10 wt%, depending on crystal size.
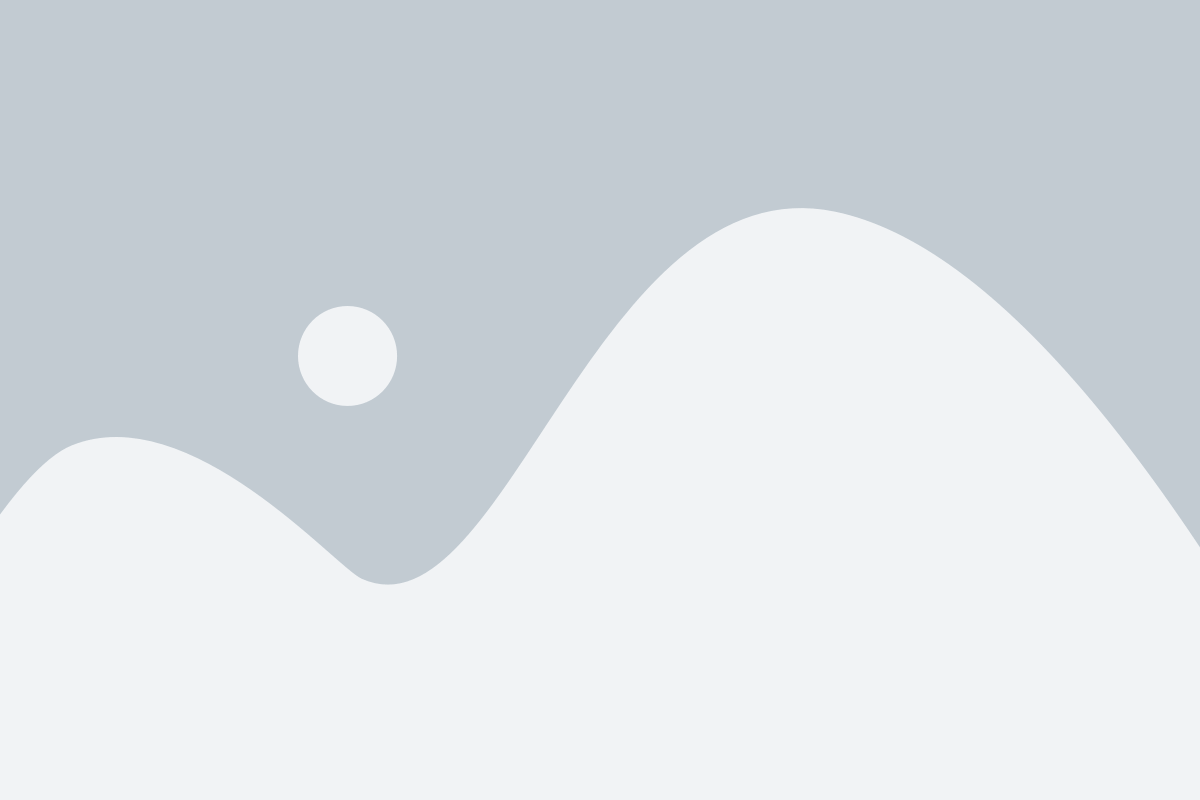
Ni Coated Diamond Powder
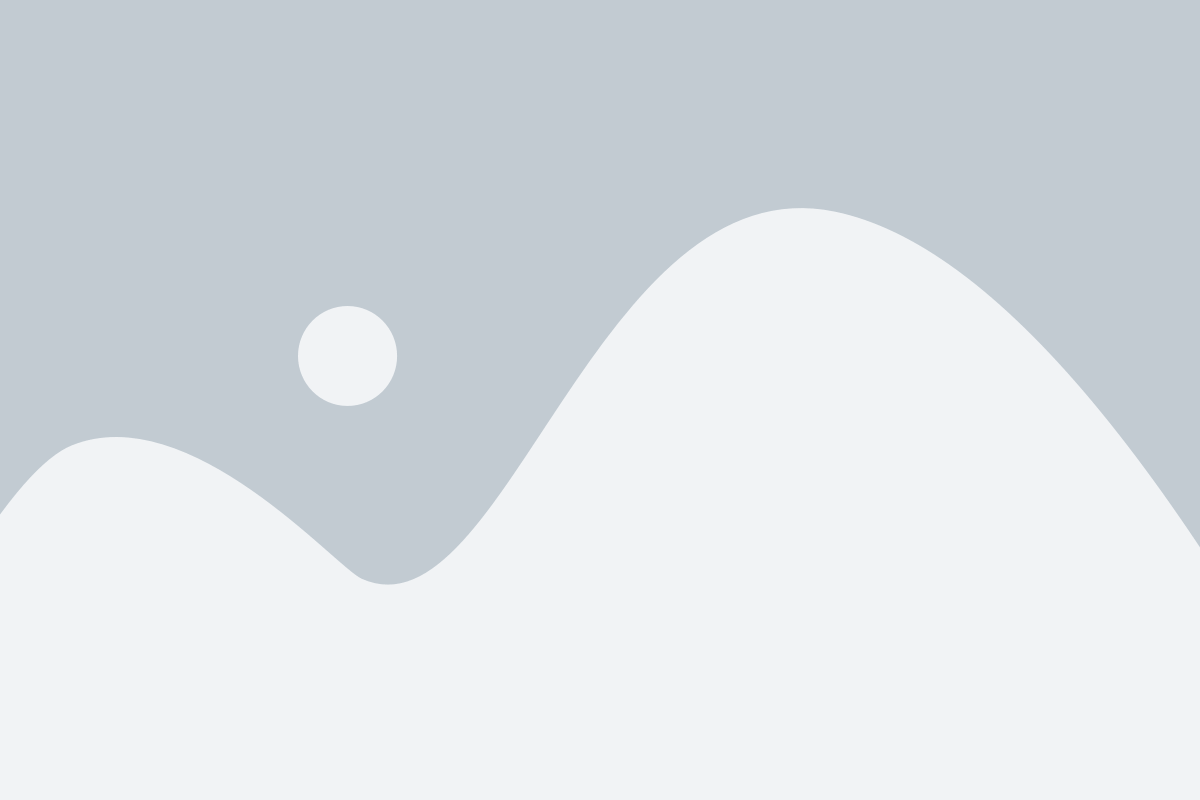
W Coated Diamond Powder
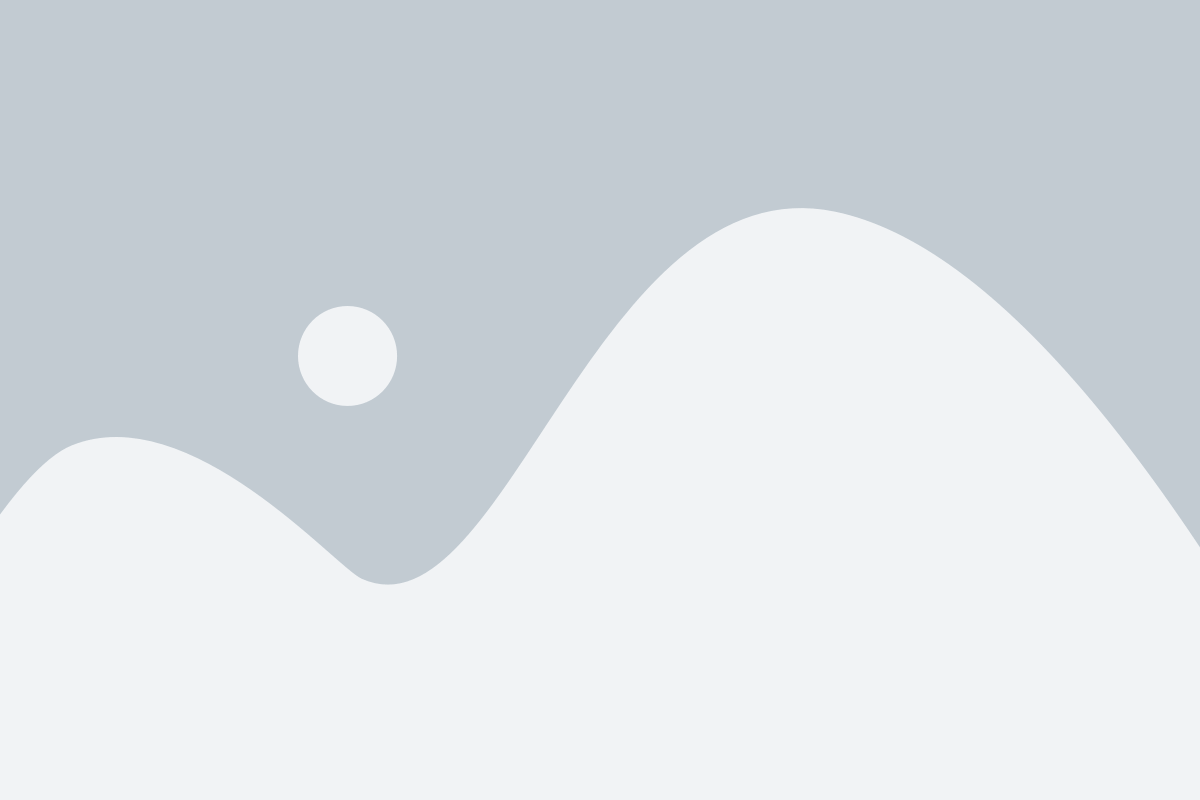
Cu Coated Diamond Powder
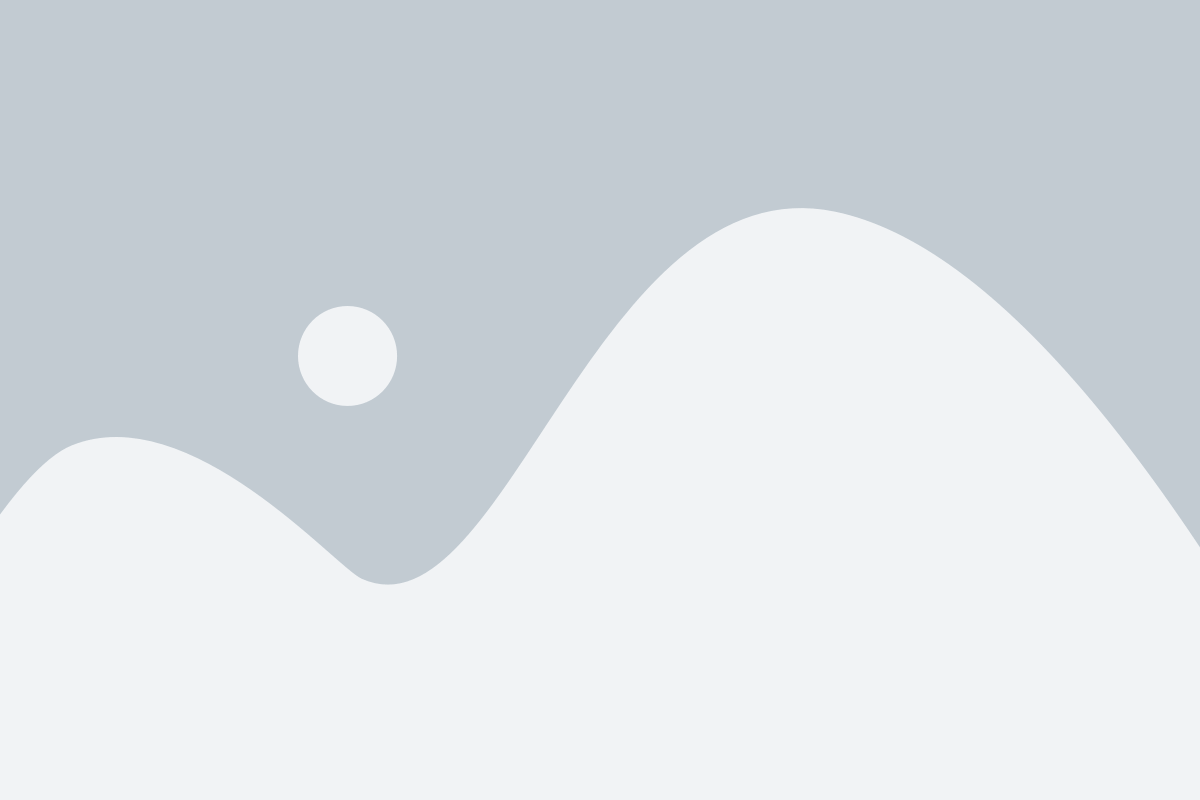
Cr Coated Diamond Powder
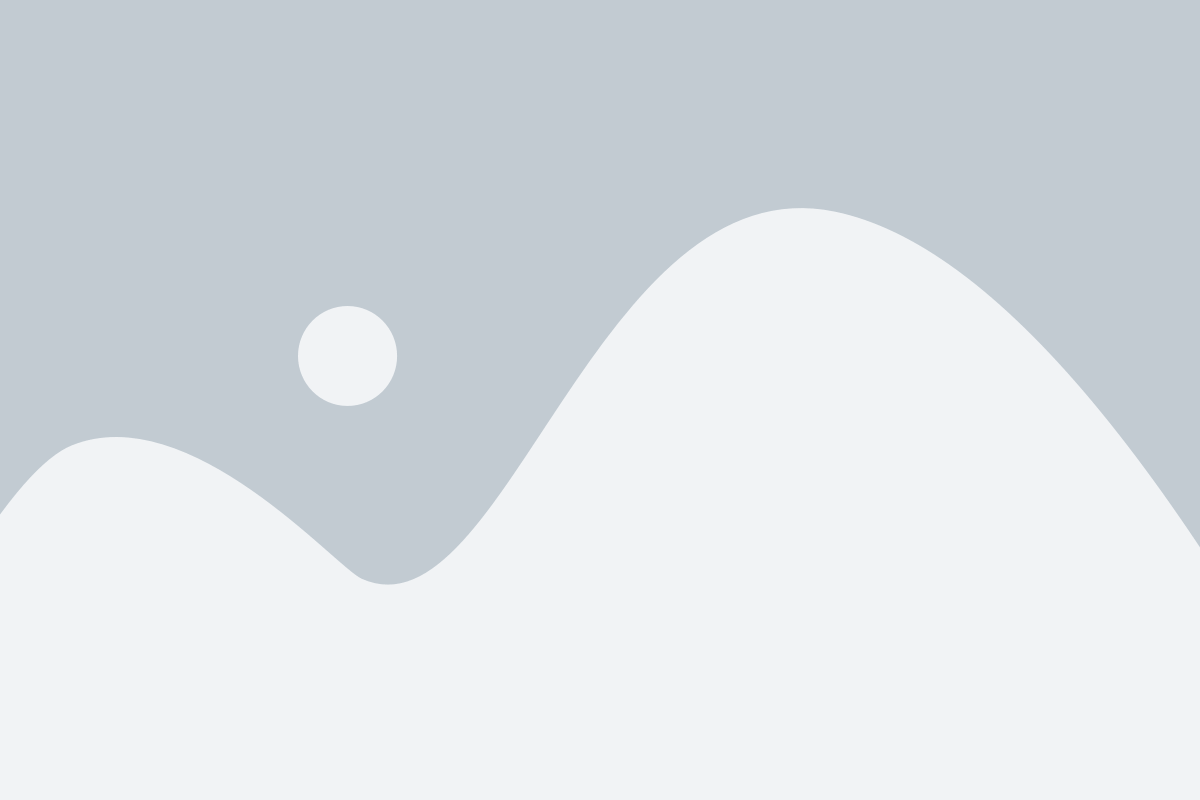
Co Coated Diamond Powder
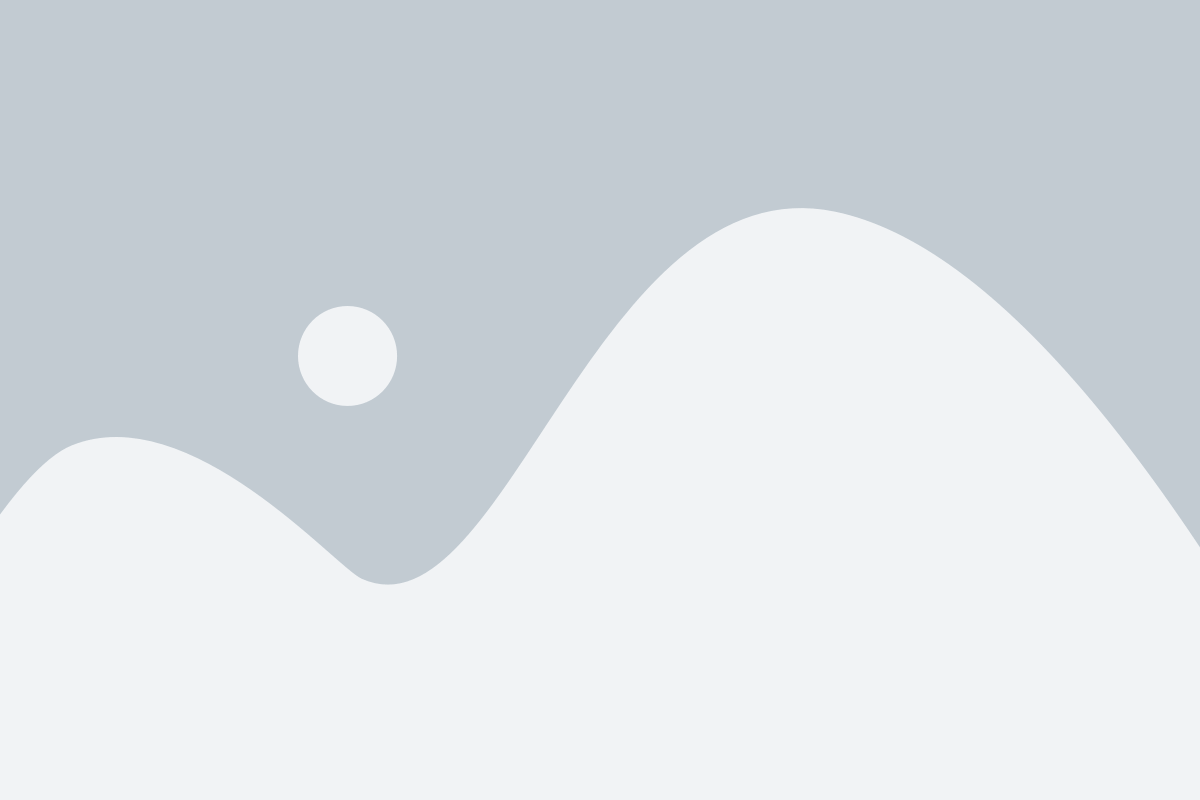
TiC Coated Diamond Powder
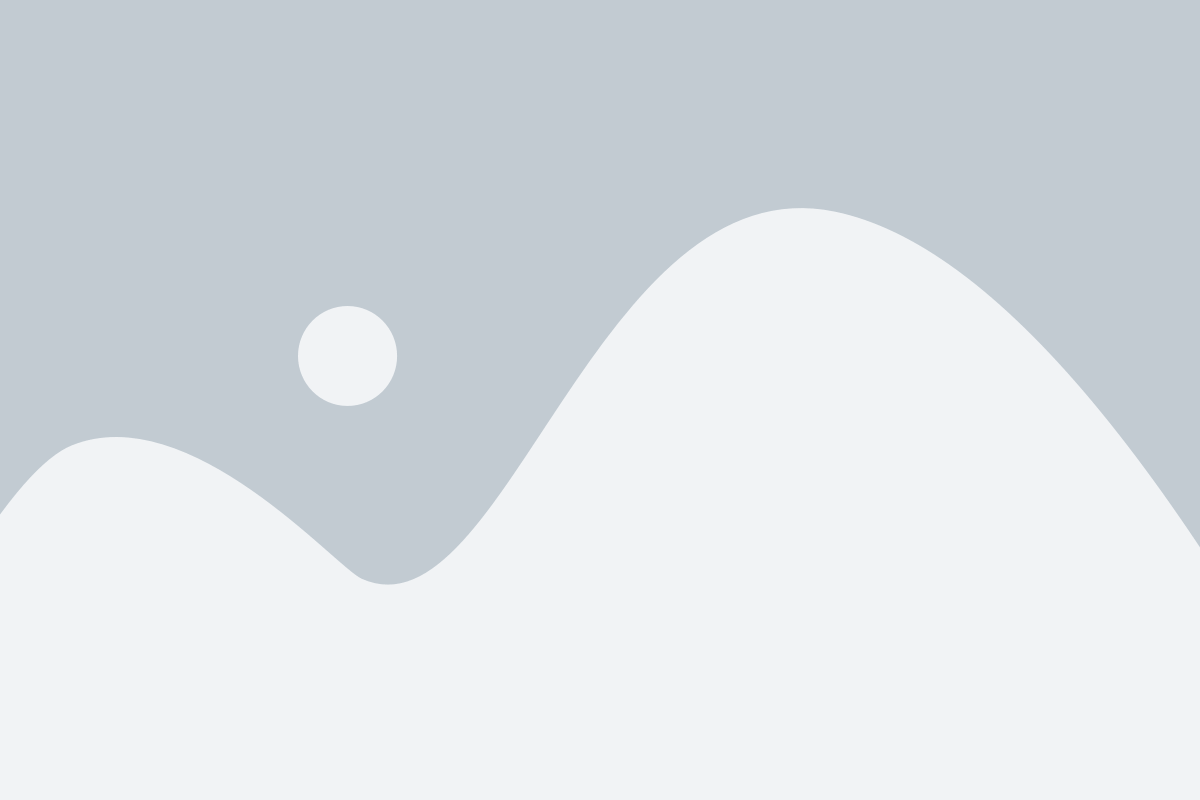
Si Coated Diamond Powder
Your Trusted Coated Diamond Powder Supplier
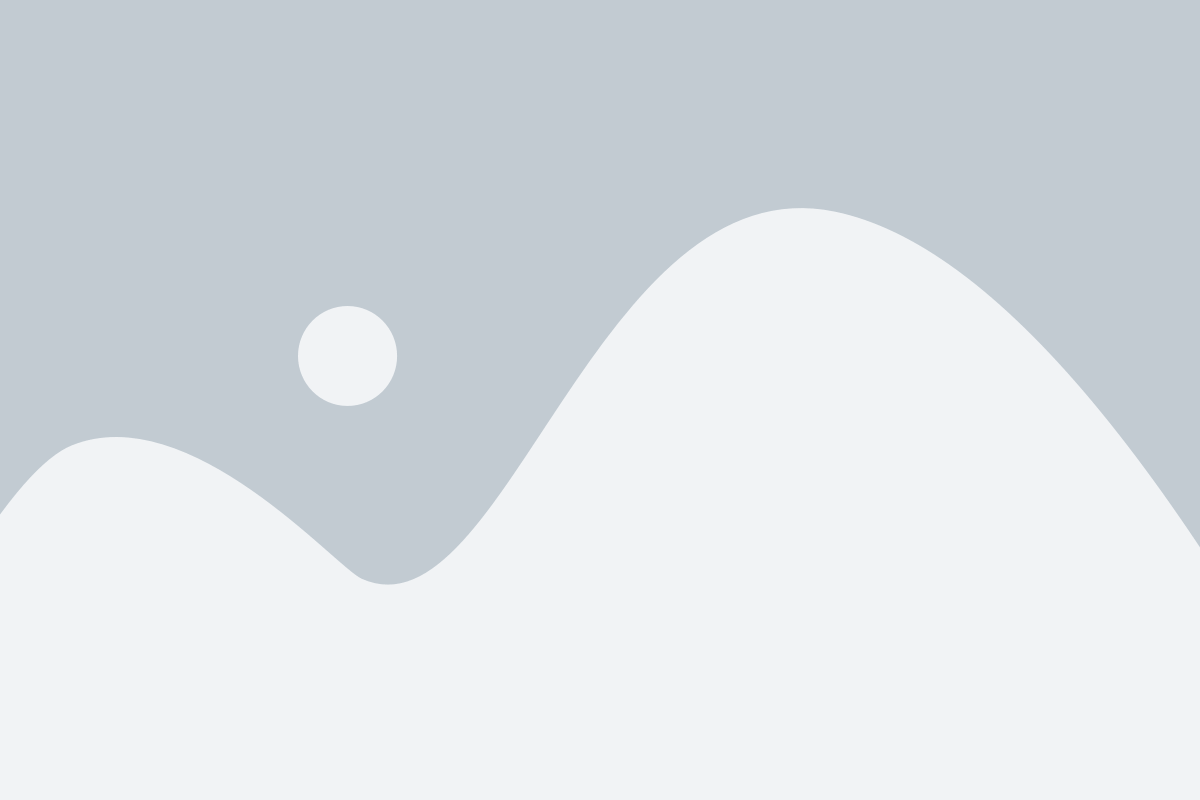
Tailor Coated Diamond Powder Solutions
Tailored Size Range: Available from 10μm to 600μm, suitable for a wide range of grinding, cutting, and drilling applications.
Enhanced Surface Properties: Each diamond particle is uniformly coated with metal layers such as Ti, Ni, W, Cr, Co, or Cu, improving bond retention, thermal stability, and oxidation resistance during high-temperature processing.
Optimised Bond Compatibility: Designed for use in metal bond, resin bond, bronze bond, and ceramic bond systems, ensuring stronger diamond-to-binder adhesion and extended tool life.
Stable Quality control: Strict control over particle size distribution, coating thickness, and surface purity ensures reliable performance and batch-to-batch consistency.
Custom Coating Options: A full range of coating materials (Ti, Ni, W, Cu, Cr, Co, TiC, Si) is available to meet different bond systems and processing requirements.
Why Choose Coated Diamond Powder from Crownkyn
At Crownkyn, we know that every tool demands the right diamond solution. Our coated diamond powder is engineered with a range of coatings and specifications to suit your bond system and application needs. Rely on us for consistent quality, expert guidance, and dependable performance in your production.
With our own dedicated manufacturing facility, we eliminate middlemen, ensuring faster production cycles, expert technical support, and responses to your inquiries within 24 hours.
Our factory-direct model delivers high-quality coated diamond powder at competitive prices, trusted by manufacturers and distributors in over 40 countries with an 85% repeat order rate.
We oversee every step of our manufacturing process, from raw diamond selection to final inspection, ensuring consistent coating quality and dependable performance for your tools.
Frequently Asked Question
Manufacturing Workshop
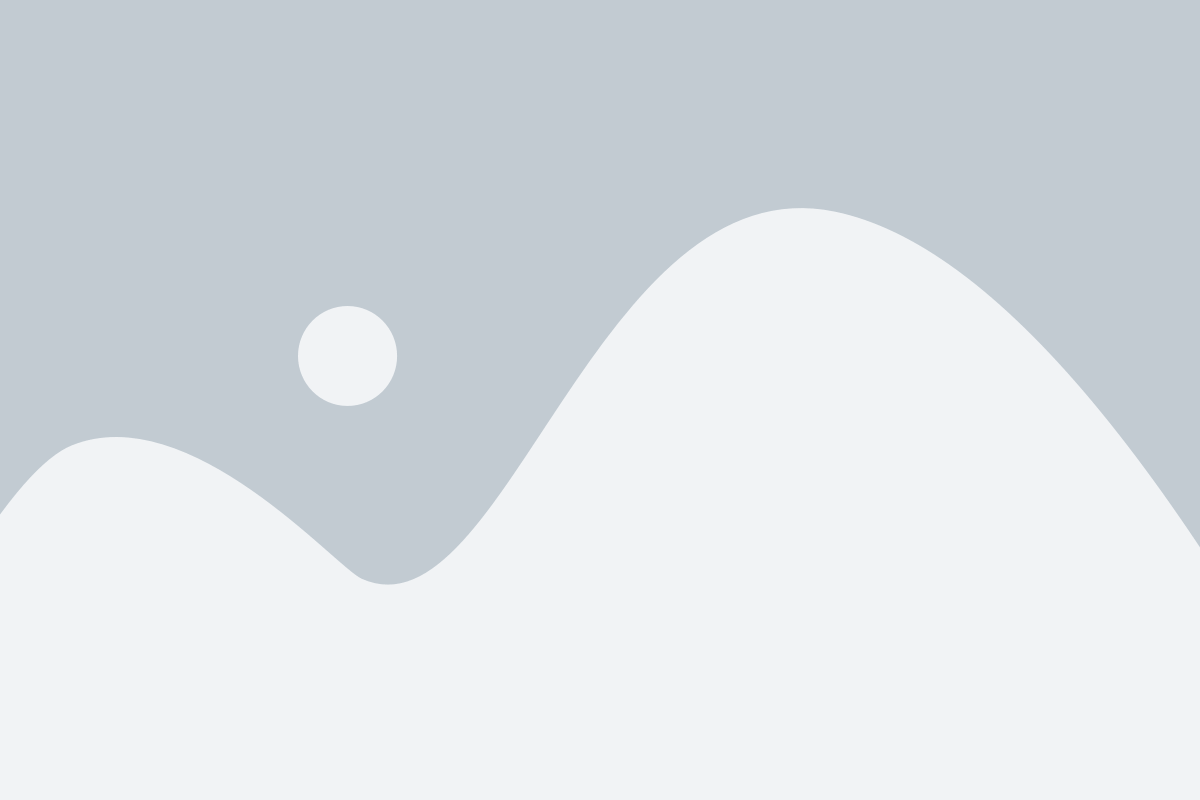
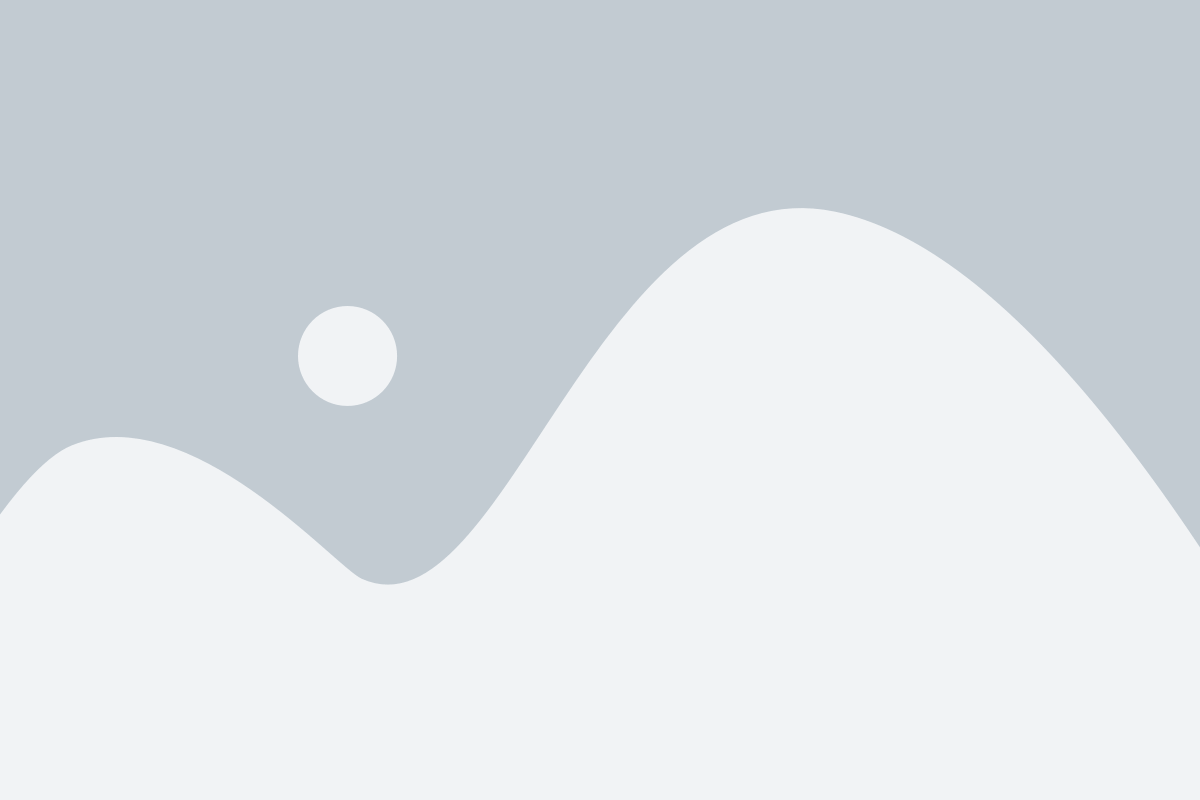
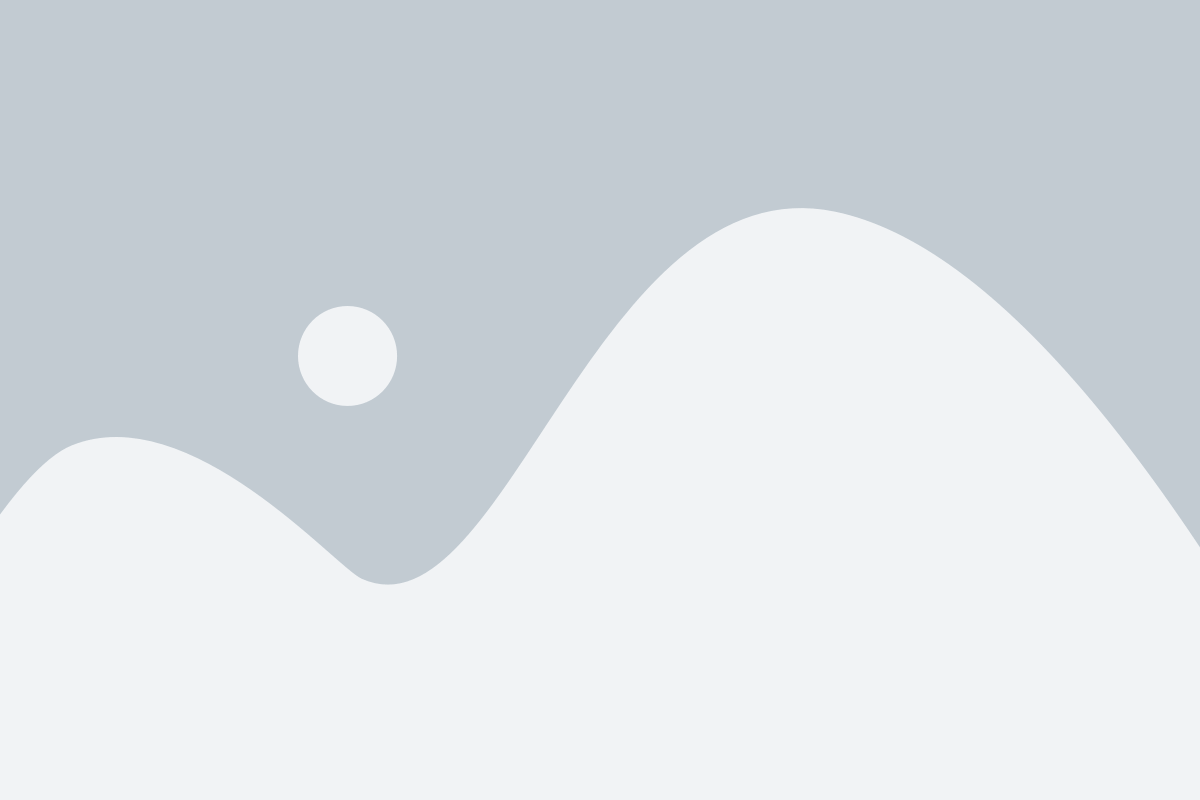
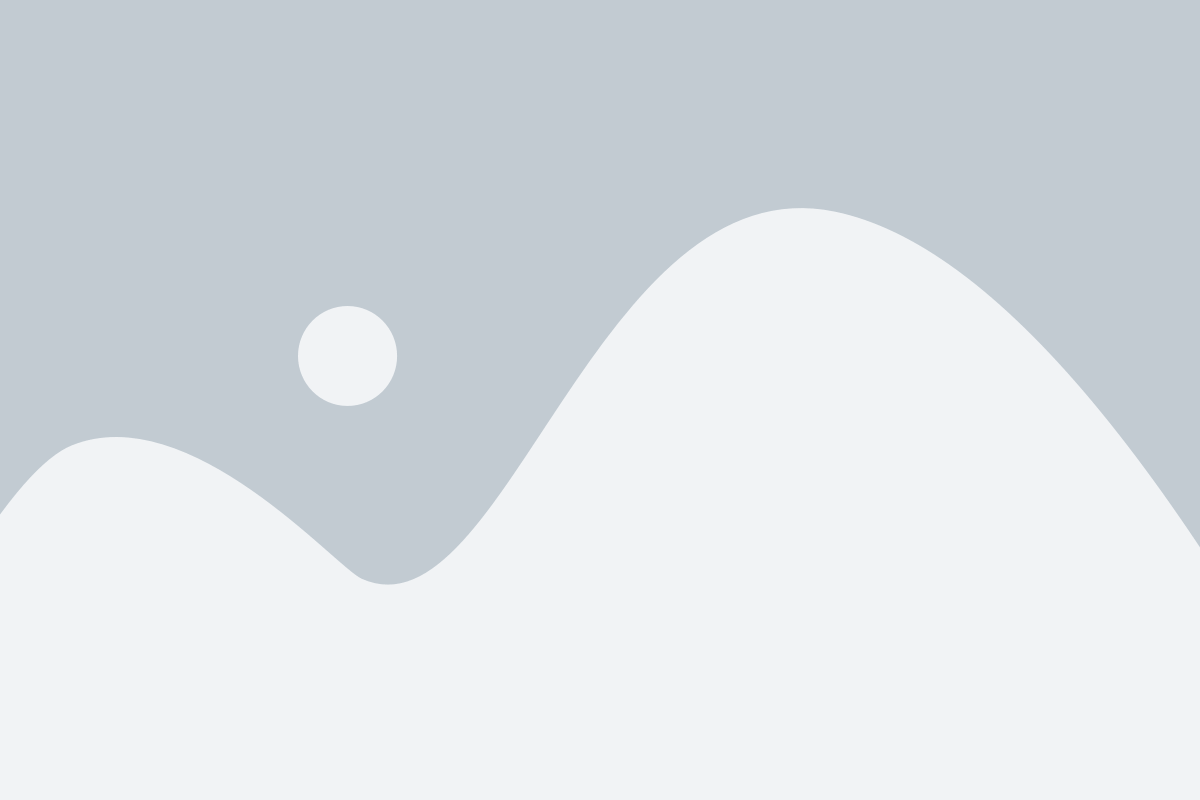
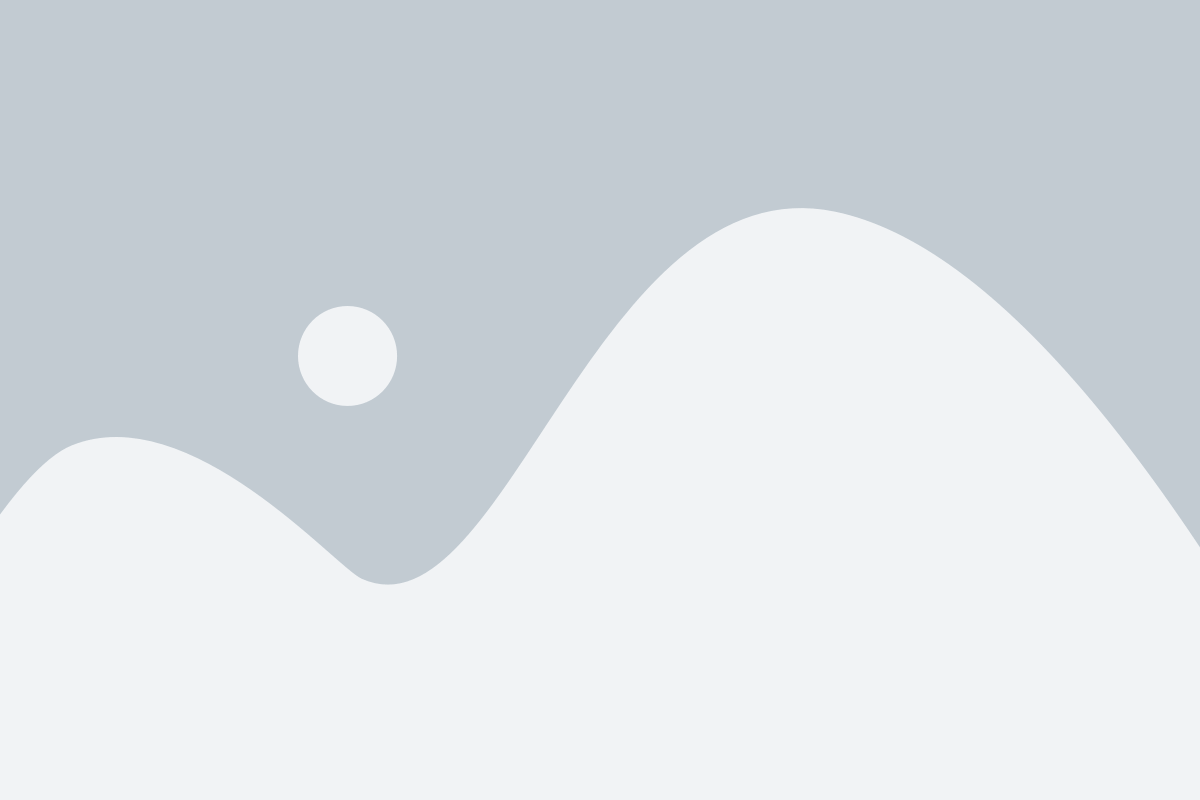
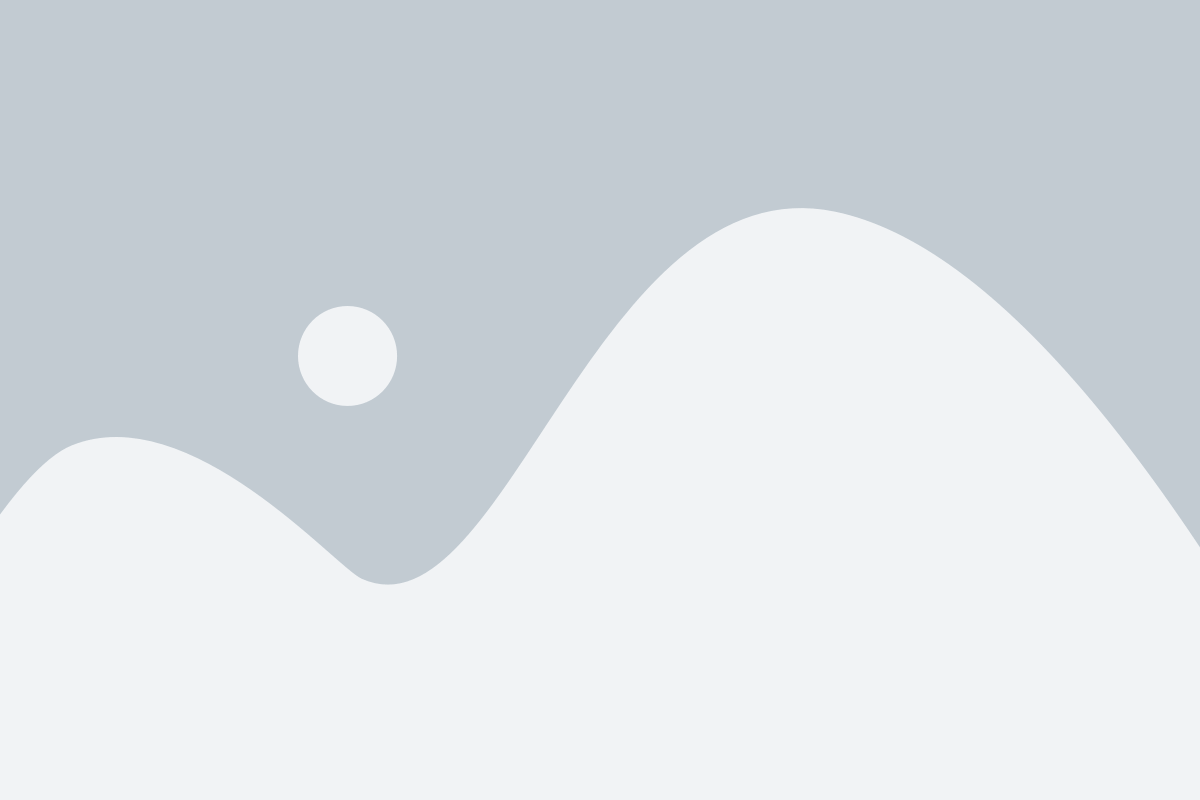
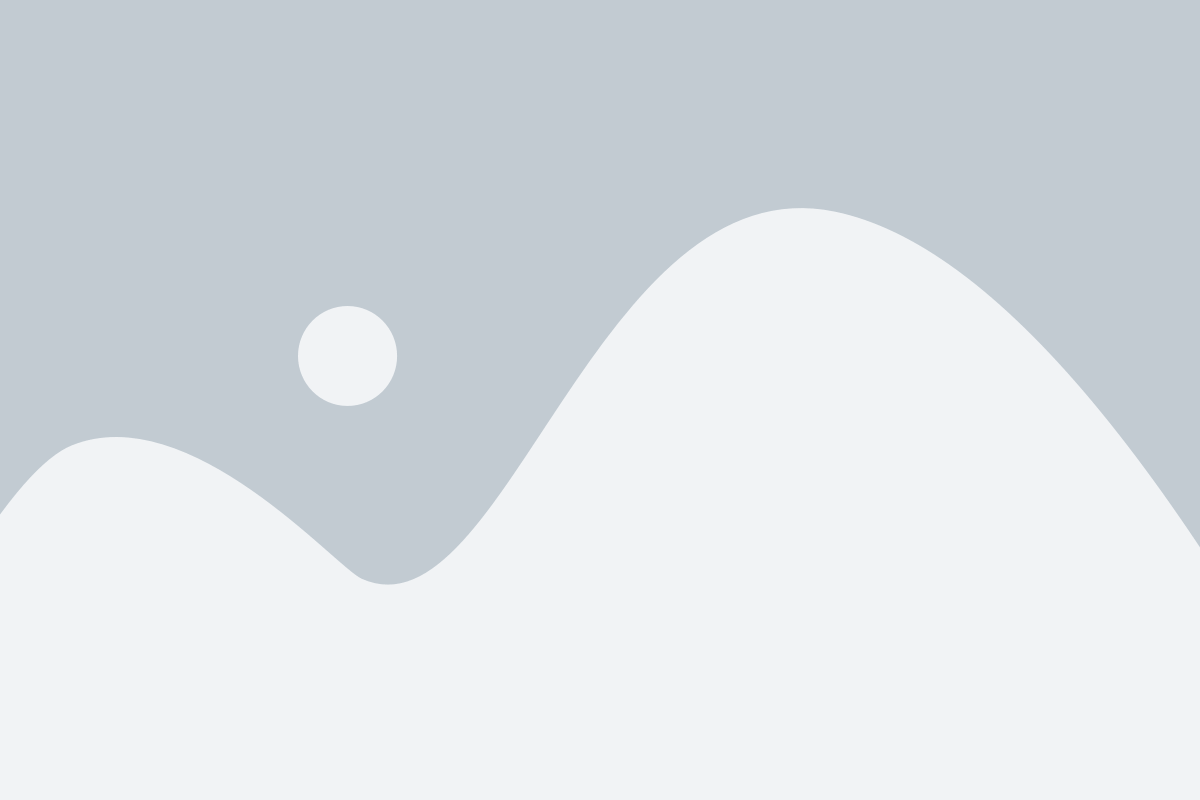
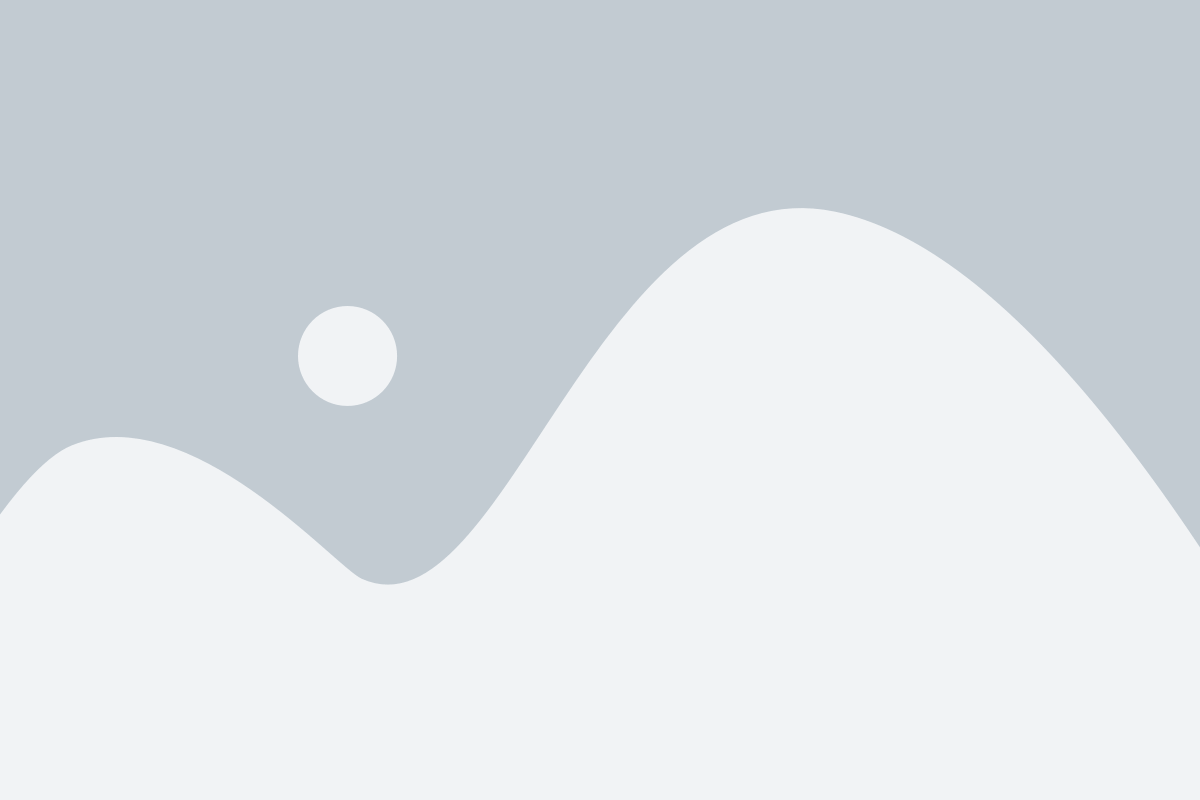
Coated Diamond Powder
The Comprehensive Guide
(2024)
Table of Contens
- 1. What is Coated Diamond Powder
- 2. Key Features and Benefits of Coatings
- 3. Coating Types and Their Functions
- 4.Available Grades, Grit Sizes, and Coating Thickness
- 5. Bond System Compatibility
- 6. Typical Applications in Various Industries
- 7. How to Select the Right Coated Diamond Powder
- 8.Sample Testing and Performance Verification
- 9.Packaging, Handling, and Storage Guidelines
What is Coated Diamond Powder?
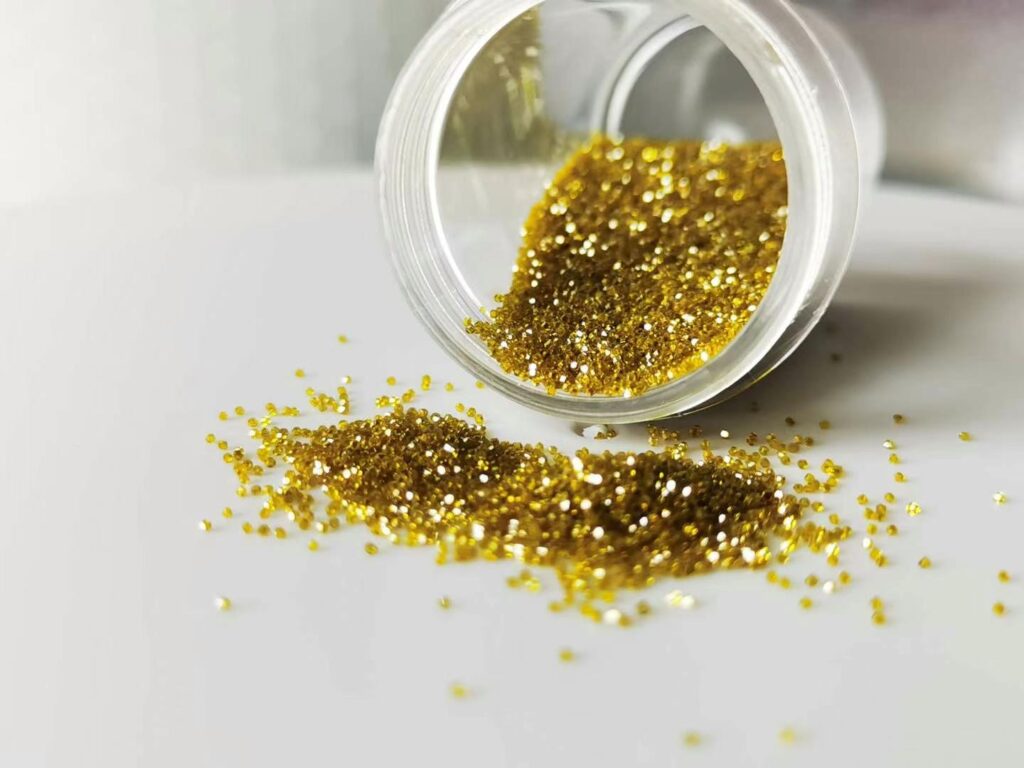
Key Features and Benefits of Coating Diamond
Enhanced Bond Retention
Improved Thermal Stability
Better Heat Dissipation
Consistent Coating Quality
Versatility Across Bond Systems
Coating Types and Their Functions
Available Grit Sizes, and Coating Thickness
Available Grit Sizes
Coating Thickness
Bond System Compatibility
Resin Bond
Vitrified Bond
Metal Bond (Sintered)
Electroplated Bond
Typical Applications in Various Industries
- Aerospace & Automotive:Grinding and cutting of tungsten carbide, ceramics, and high-silicon aluminium alloys for engine components, brakes, and structural parts.
- Electronics & Semiconductors:Precision lapping and polishing of optical glass, sapphire, and electronic substrates for displays, wafers, and sensors.
- Construction & Stone Processing:Cutting and shaping of granite, marble, and engineered stones in construction materials and decorative applications.
- Oil & Gas / Geology:Drilling and coring of hard rock and composites with high wear resistance and thermal stability tools for exploration equipment.
- Tool Manufacturing:Production of resin, metal, vitrified, and electroplated diamond tools for grinding, drilling, and cutting ultra-hard materials.
How to Select the Right Coated Diamond Powder
STEP 1
Match the Bond System
STEP 2
Choose the Appropriate Grit Size
STEP 3
Choose the Right Grit Size
STEP 4
Determine Coating Thickness
STEP 5
Consult Technical Experts
Quality Control and Consistency
Uniform Coating Quality: Advanced deposition techniques ensure an even and consistent coating layer on each particle, verified by SEM and thickness measurement, for reliable bond retention and thermal stability.
Precise Size and Shape Control: Every batch is graded with laser particle size analysers and precision sieving to achieve uniform particle size distribution and optimal crystal shape, ensuring predictable tool performance.
High Purity Standards: ICP and XRF testing are used to monitor and minimise impurities, preventing contamination and maintaining the integrity of your tools during high-temperature processing.
Consistent Batch Performance: All production lots are subject to magnetic separation, visual inspection, and sample testing to guarantee stable coating adhesion, particle quality, and performance from batch to batch.
Sample Testing and Performance Verification
Custom Sample Preparation
Application-Based Testing
Technical Support Service
Performance Feedback Loop
Packaging, Handling, and Storage Guidelines
- Moisture-proof and anti-static containers
- Sealed plastic bottles or vacuum-sealed foil bags
- Outer cartons for bulk protection
-
Custom packaging available on request
- Wear gloves and masks to avoid inhalation and skin contact
- Use clean, dry tools when opening or transferring
- Handle in a clean, controlled environment
- Keep sealed in original packaging until use
- Store in a cool, dry, and well-ventilated place
- Avoid moisture, sunlight, and extreme temperatures
An expert of agriculture protection textile specialist.
In the past 26 years, we’ve supported 100+ clients across 35 countries, including diamond tools manufacturers and synthetic diamond powder distributors to significantly enhance their product quality and efficiency. The purpose of article is to share insights on advanced abrasive solutions, helping you produce higher quality diamond tools with improved performance and durability.
Coated Diamond Powder
Engineered Coated Diamond Powder for Enhanced Bonding and Tool Life
Improve Grinding Stability with Coated Diamond Powder
Coated diamond powder is designed to improve bond retention, thermal stability, and overall grinding efficiency. Crownkyn’s coated diamond features a uniform metal or ceramic coating (such as Ni, Ti, Cu, Cr, W, Co), enhancing the interface between the diamond and the bond system, especially in resin, metal, and vitrified bond tools.
Produced with strict control over coating thickness and coverage uniformity, our coating diamond powder ensures stable performance and extended tool life in demanding grinding and cutting applications. Choose Crownkyn for coated abrasive solutions that deliver enhanced durability and processing efficiency.
We can provide customized plating of metals such as aluminum (AI), molybdenum (Mo), zirconium (Zr), silicon (Si), copper-tin alloy (CuSn), and copper-chromium alloy (CuCr) on diamond surfaces according to customer requirements.
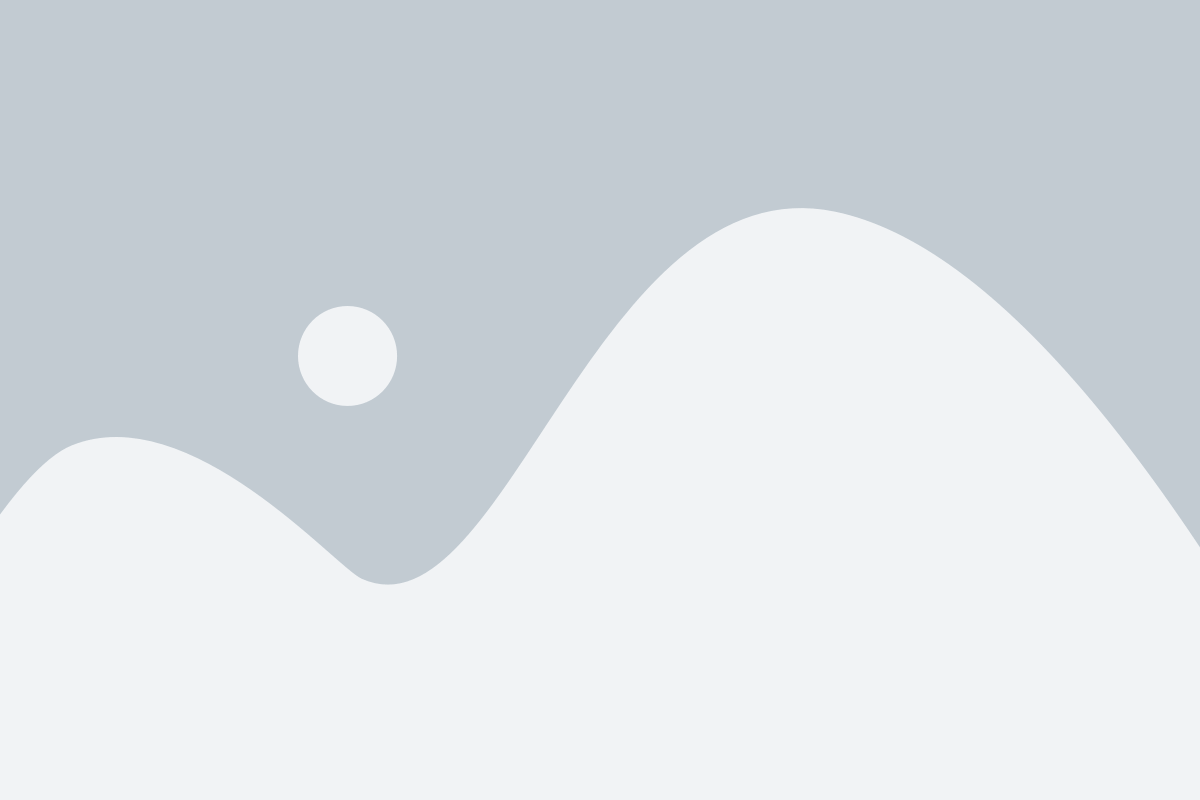
Ti Coated Diamond Powder
Characteristic: Titanium coating diamond powder provides excellent oxidation resistance and improves thermal stability. It enhances bond retention and increases diamond protrusion by improving wettability. The coating does not degrade the diamond surface or strength. Titanium content ranges from 1 wt% to 10 wt%, depending on crystal size.
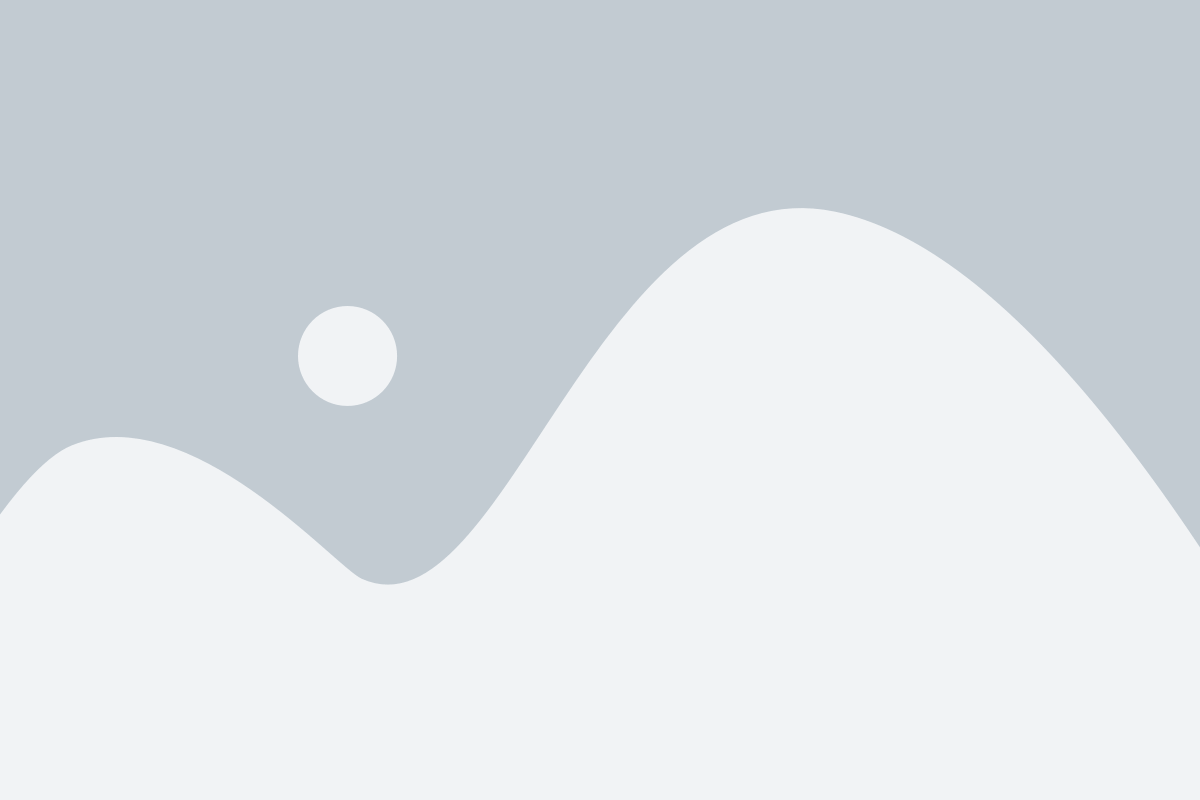
Ni Coated Diamond Powder
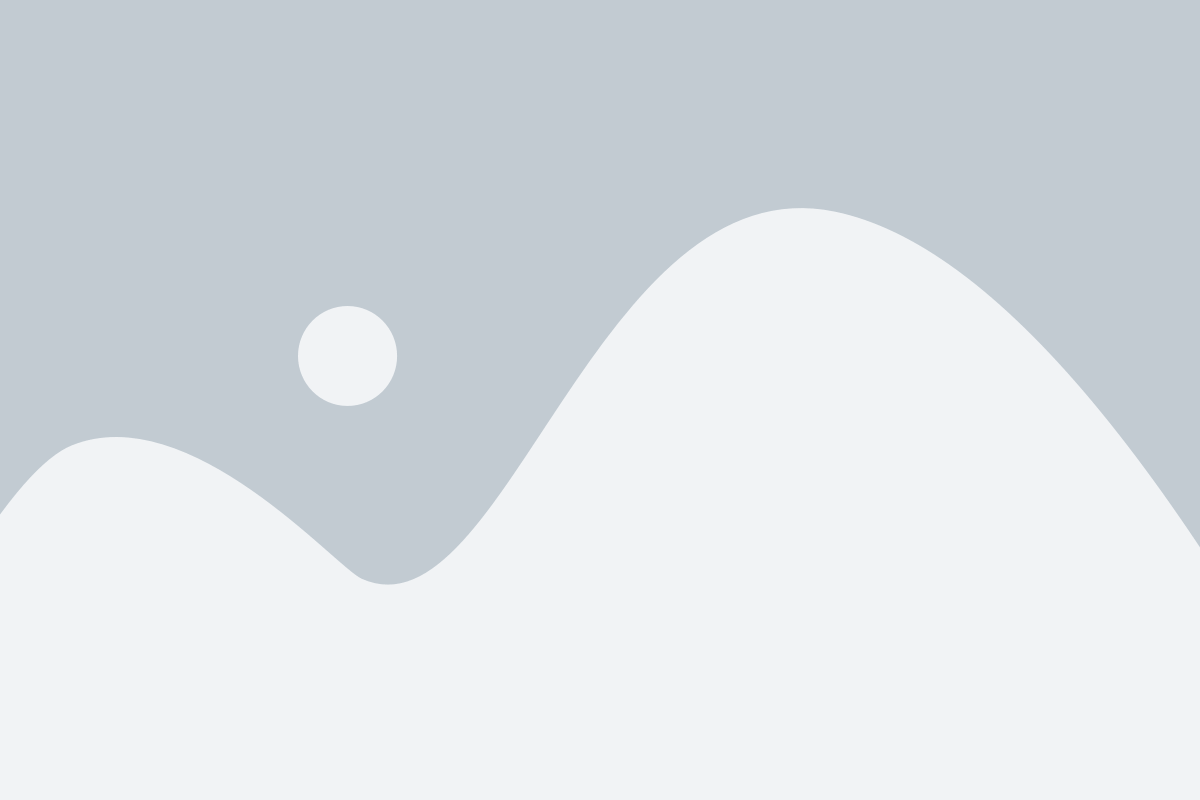
W Coated Diamond Powder
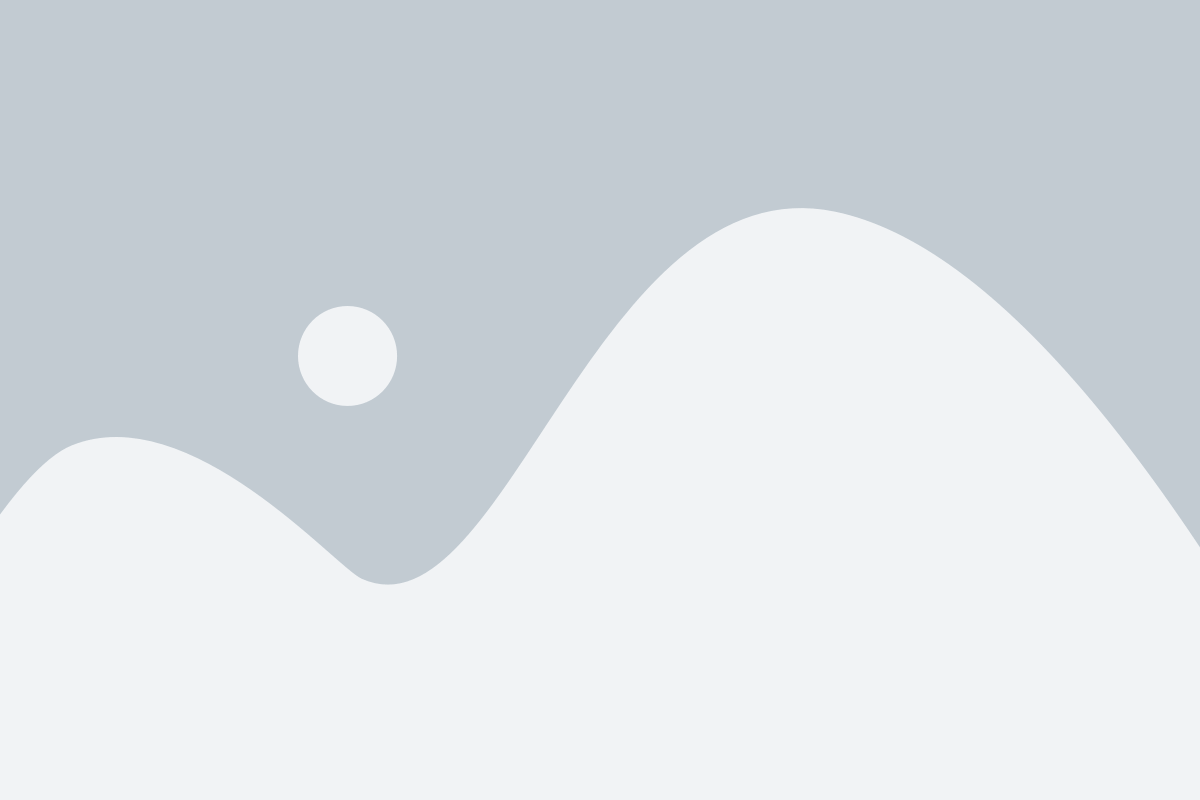
Cu Coated Diamond Powder
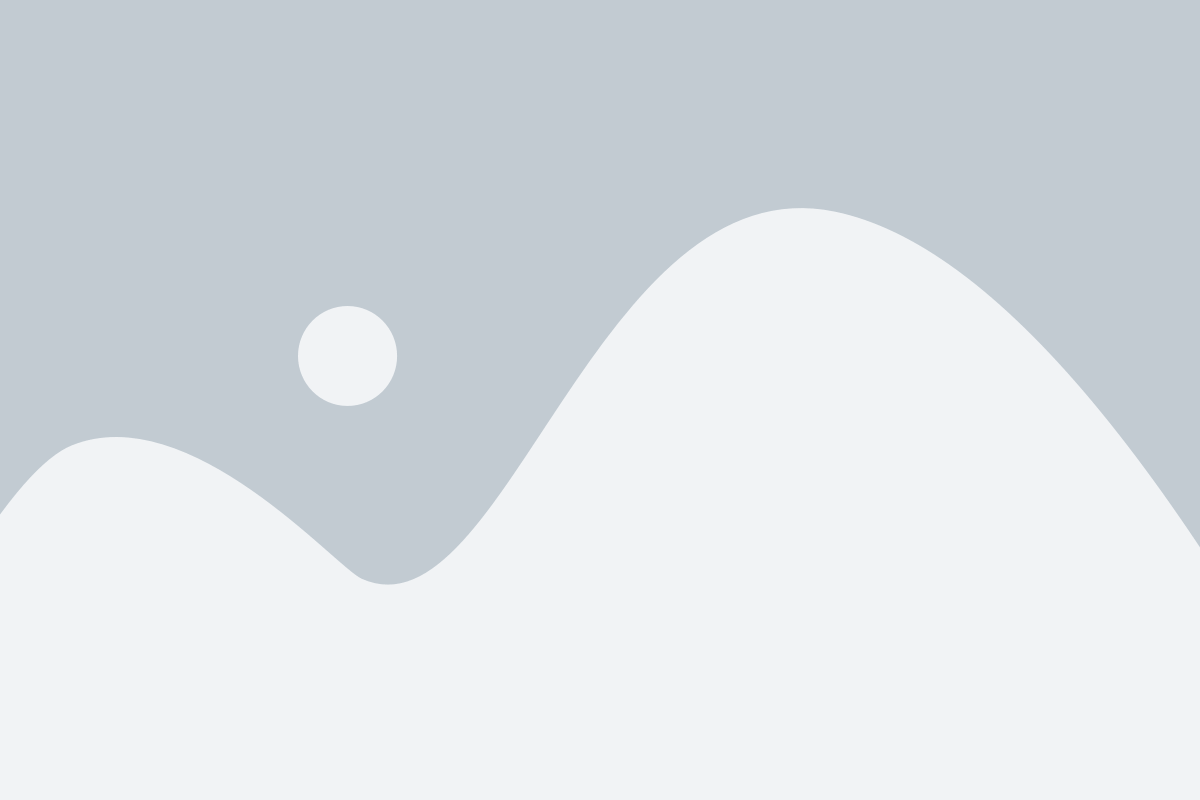
Cr Coated Diamond Powder
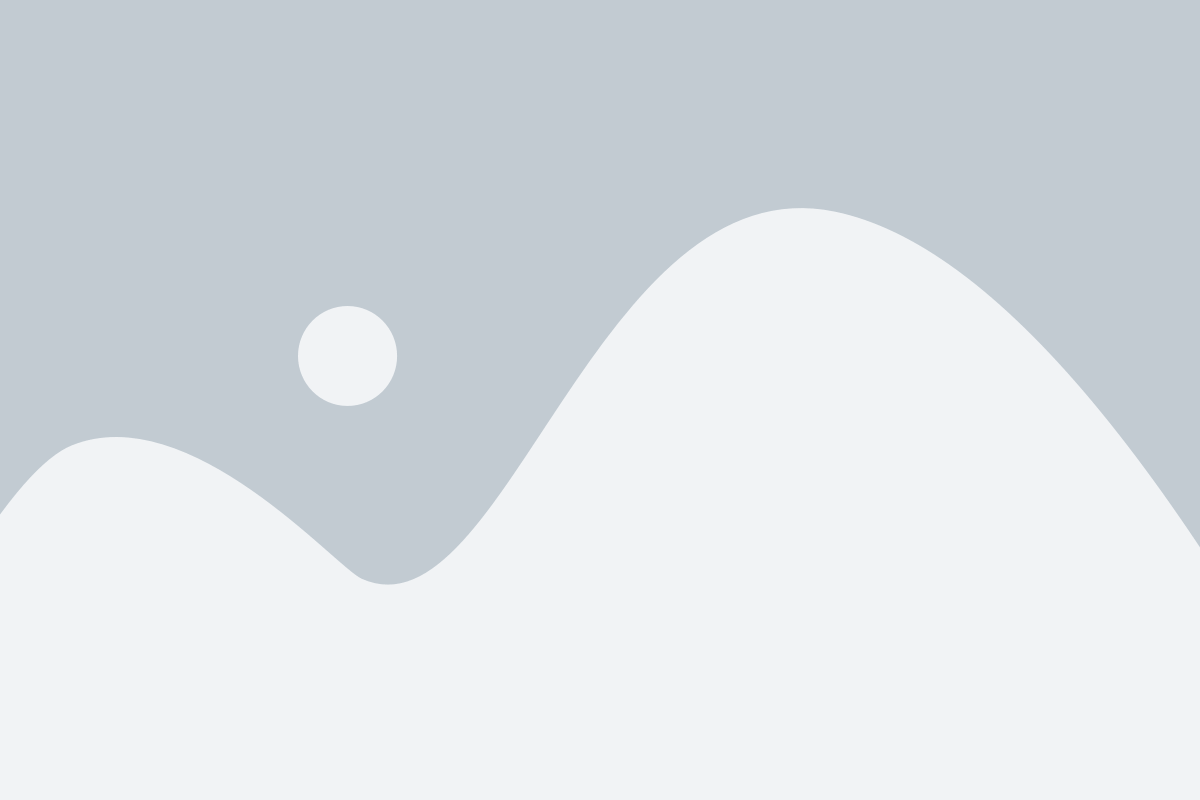
Co Coated Diamond Powder
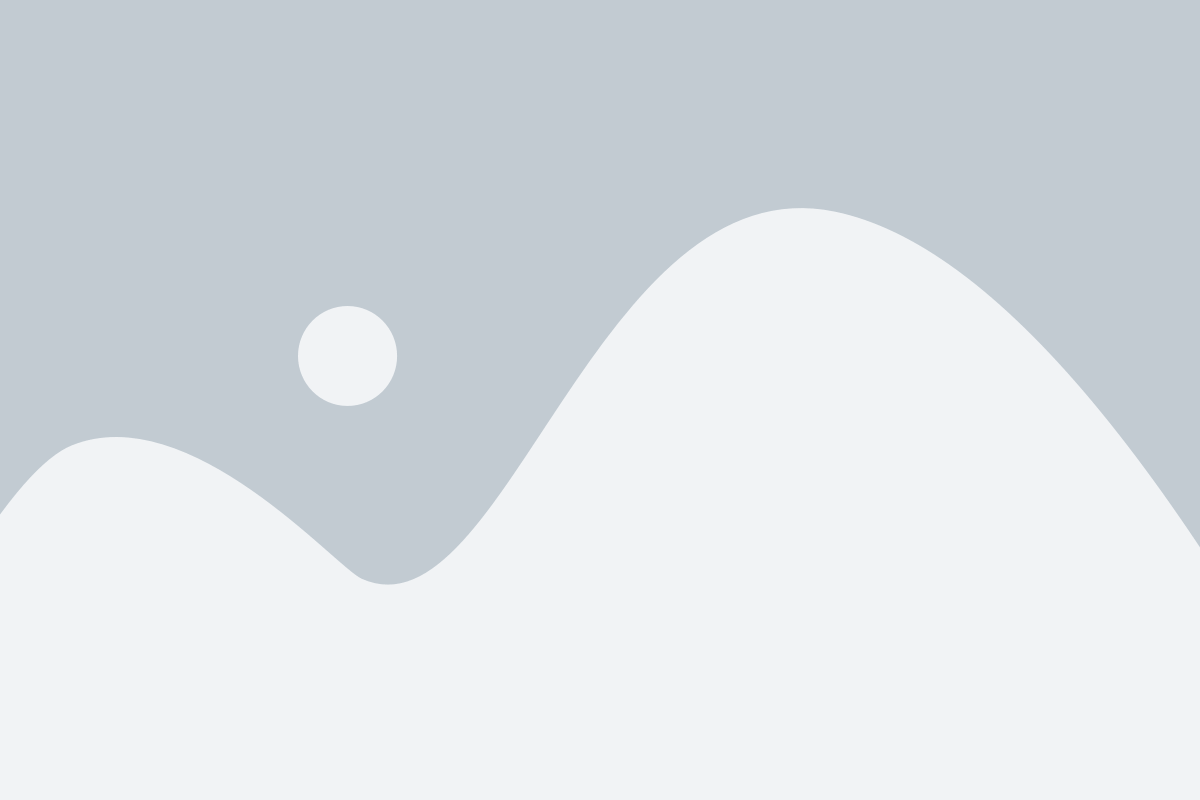
TiC Coated Diamond Powder
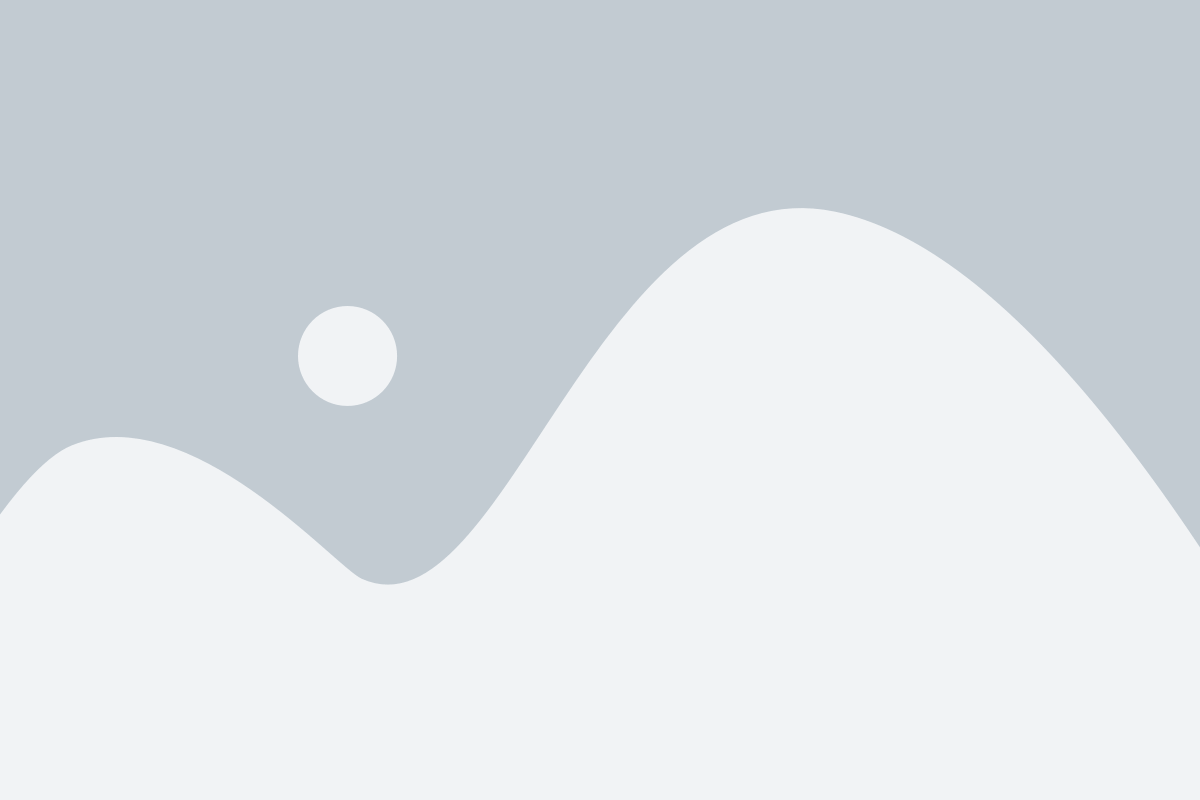
Si Coated Diamond Powder
Your Trusted Coated Diamond Powder Supplier
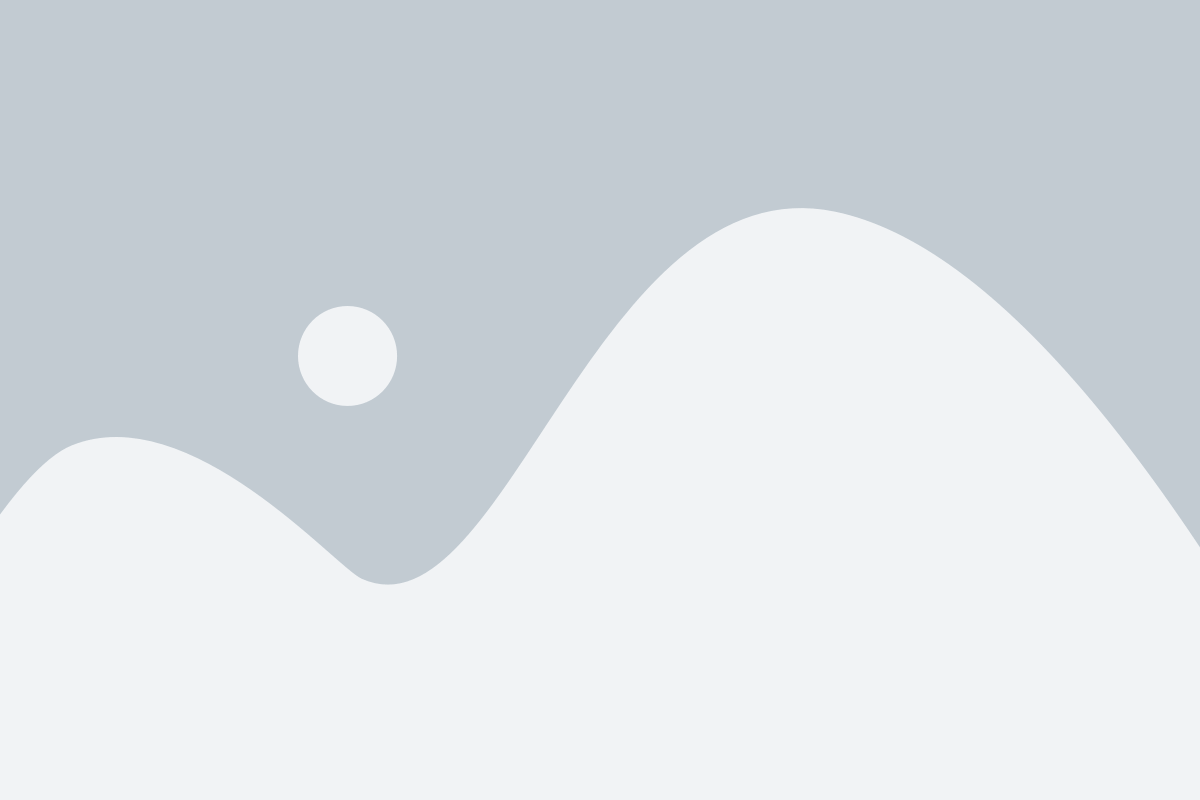
Tailor Coated Diamond Powder Solutions
Tailored Size Range: Available from 10μm to 600μm, suitable for a wide range of grinding, cutting, and drilling applications.
Enhanced Surface Properties: Each diamond particle is uniformly coated with metal layers such as Ti, Ni, W, Cr, Co, or Cu, improving bond retention, thermal stability, and oxidation resistance during high-temperature processing.
Optimised Bond Compatibility: Designed for use in metal bond, resin bond, bronze bond, and ceramic bond systems, ensuring stronger diamond-to-binder adhesion and extended tool life.
Stable Quality control: Strict control over particle size distribution, coating thickness, and surface purity ensures reliable performance and batch-to-batch consistency.
Custom Coating Options: A full range of coating materials (Ti, Ni, W, Cu, Cr, Co, TiC, Si) is available to meet different bond systems and processing requirements.
Why Choose Coated Diamond Powder from Crownkyn
At Crownkyn, we know that every tool demands the right diamond solution. Our coated diamond powder is engineered with a range of coatings and specifications to suit your bond system and application needs. Rely on us for consistent quality, expert guidance, and dependable performance in your production.
With our own dedicated manufacturing facility, we eliminate middlemen, ensuring faster production cycles, expert technical support, and responses to your inquiries within 24 hours.
Our factory-direct model delivers high-quality coated diamond powder at competitive prices, trusted by manufacturers and distributors in over 40 countries with an 85% repeat order rate.
We oversee every step of our manufacturing process, from raw diamond selection to final inspection, ensuring consistent coating quality and dependable performance for your tools.
Frequently Asked Question
Manufacturing Workshop
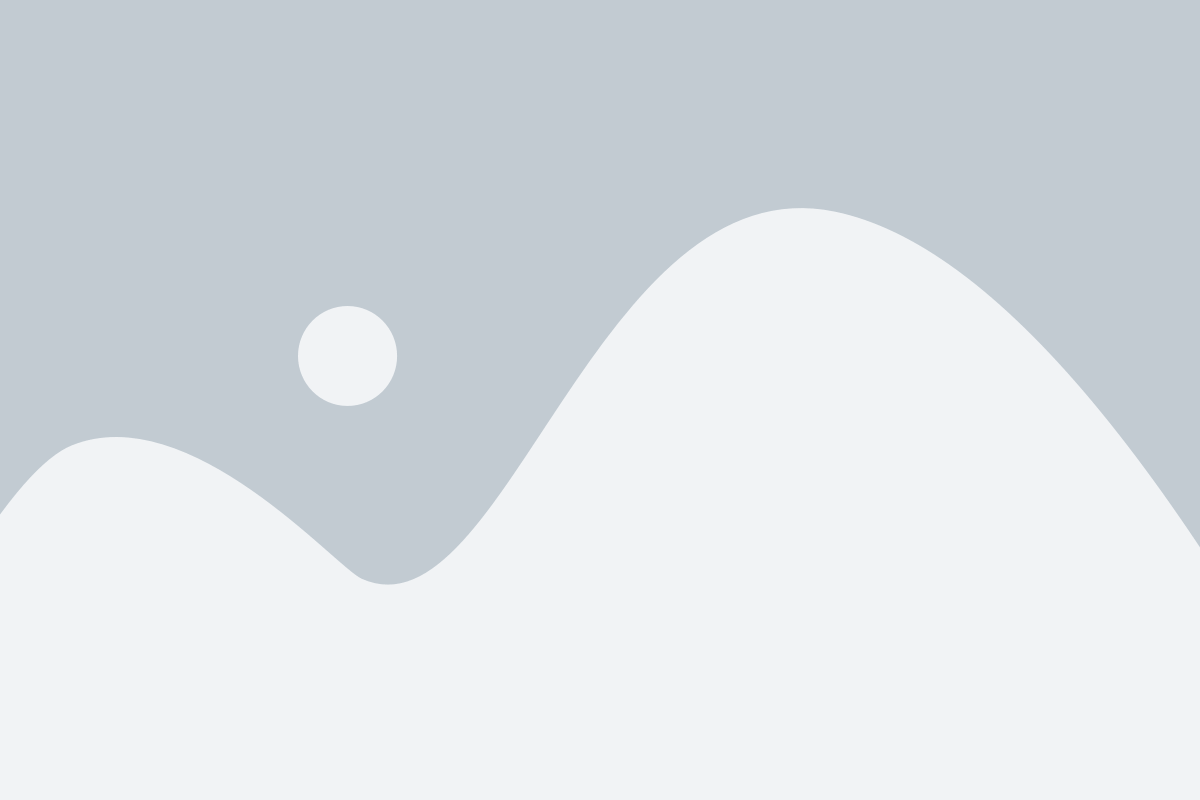
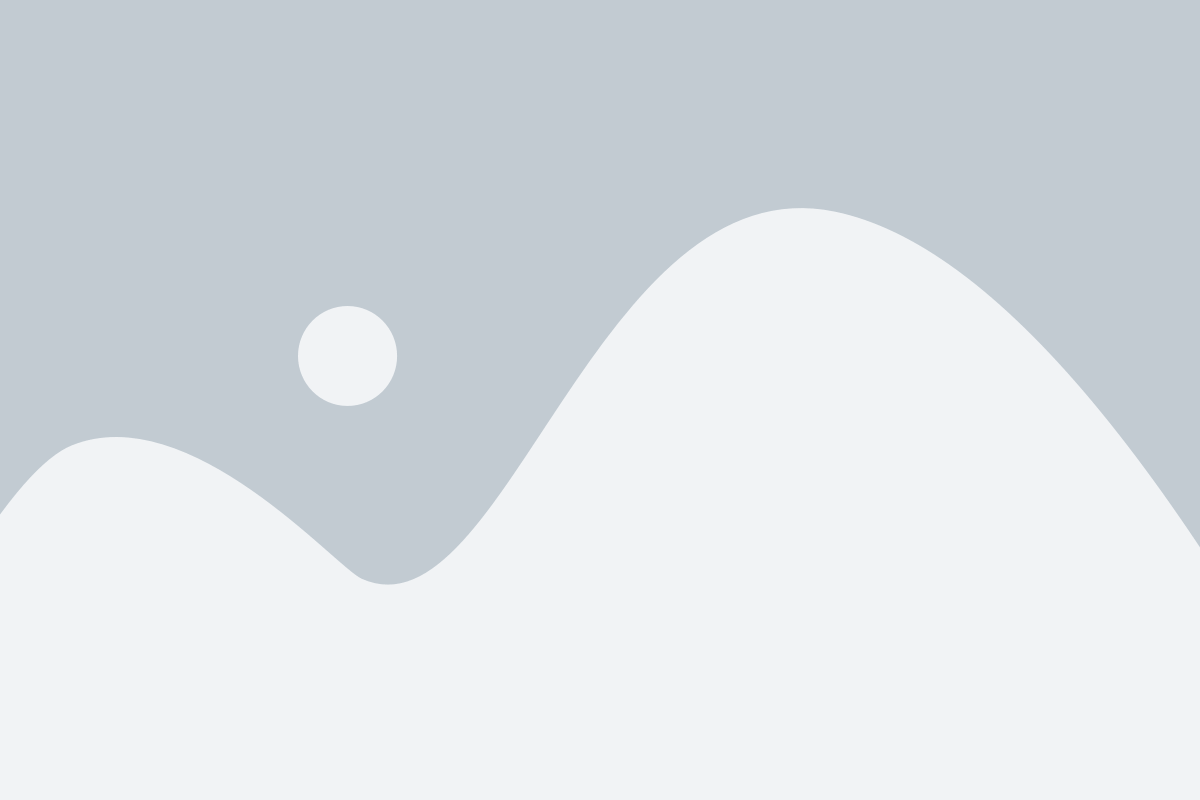
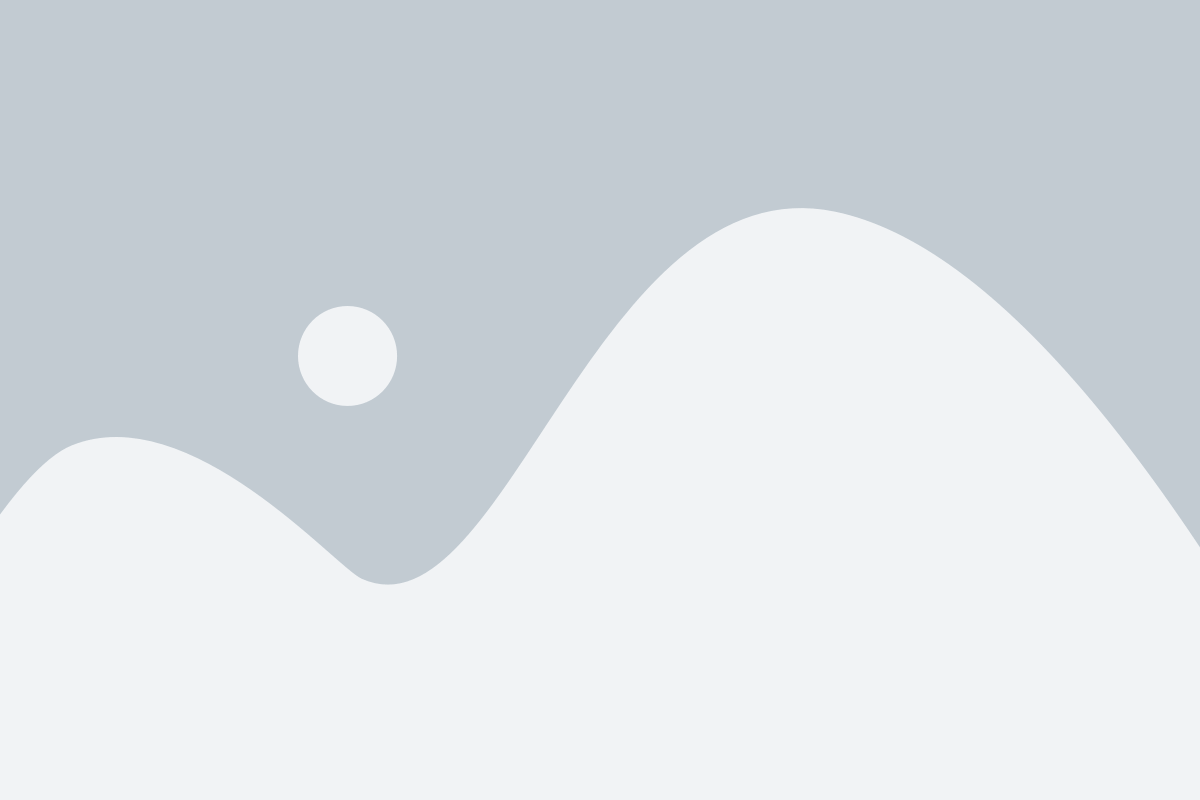
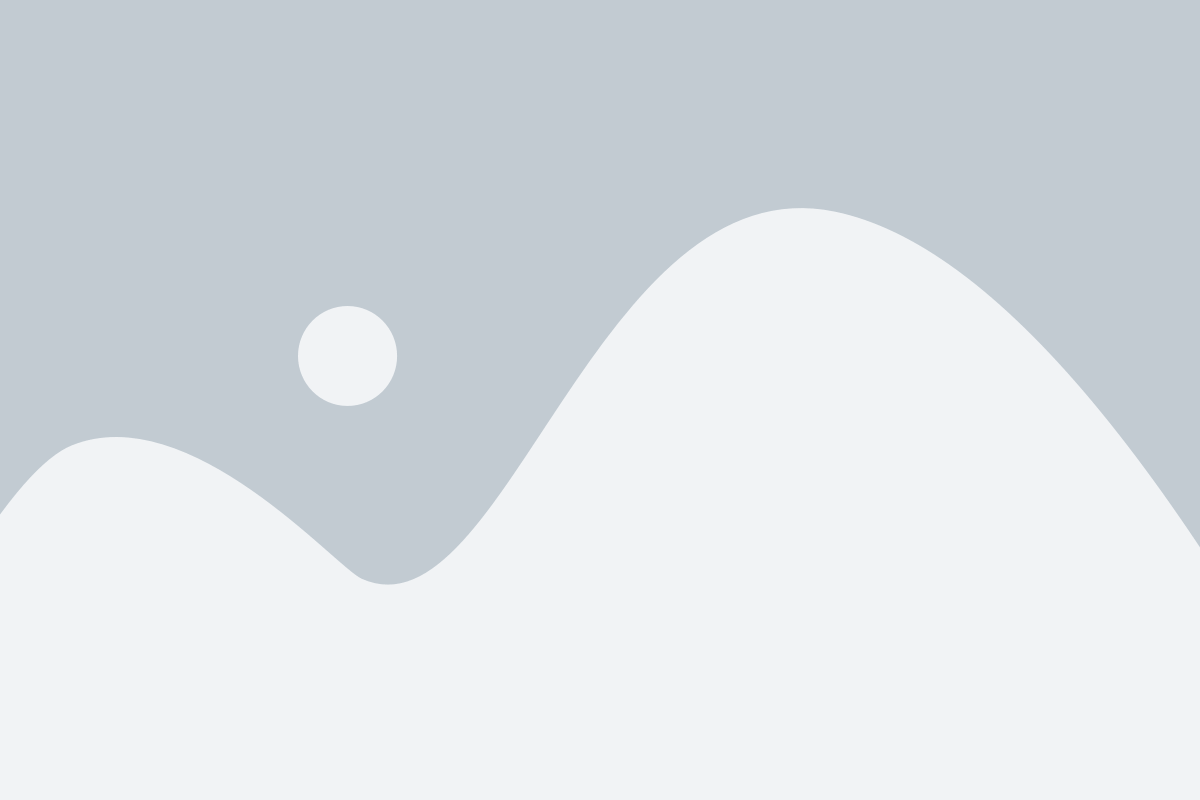
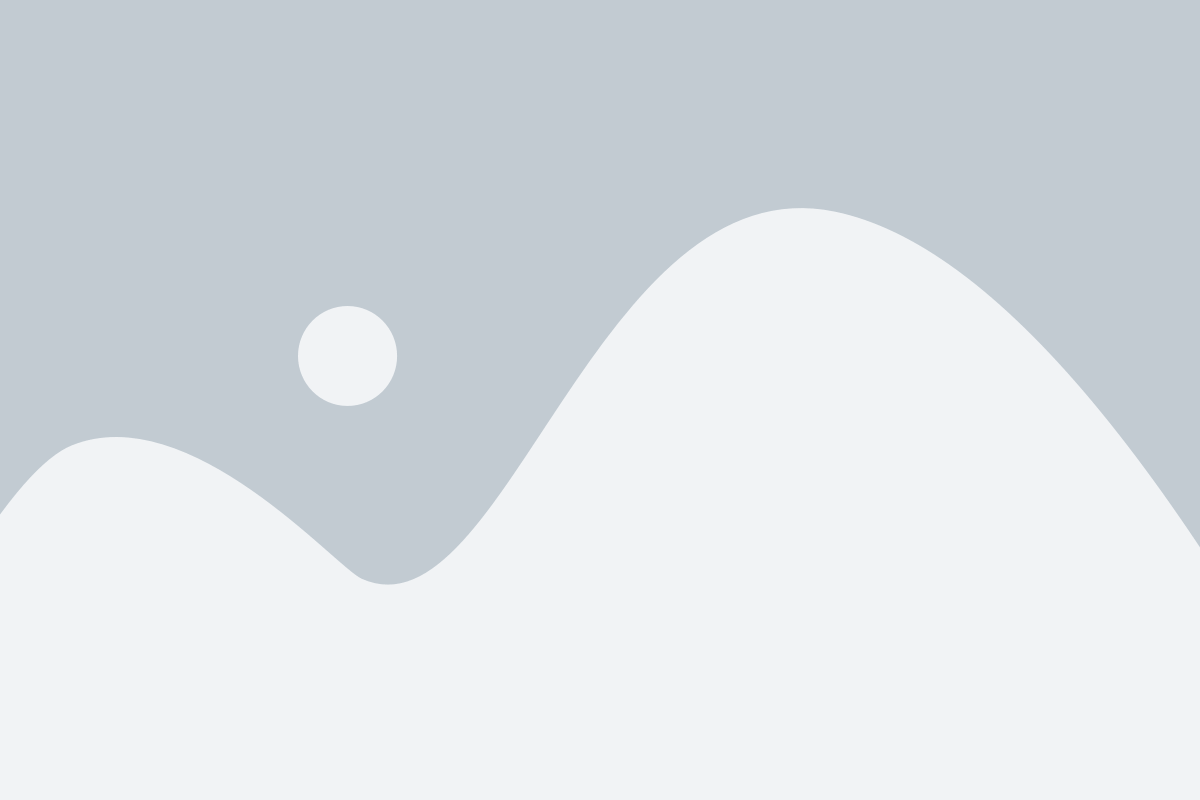
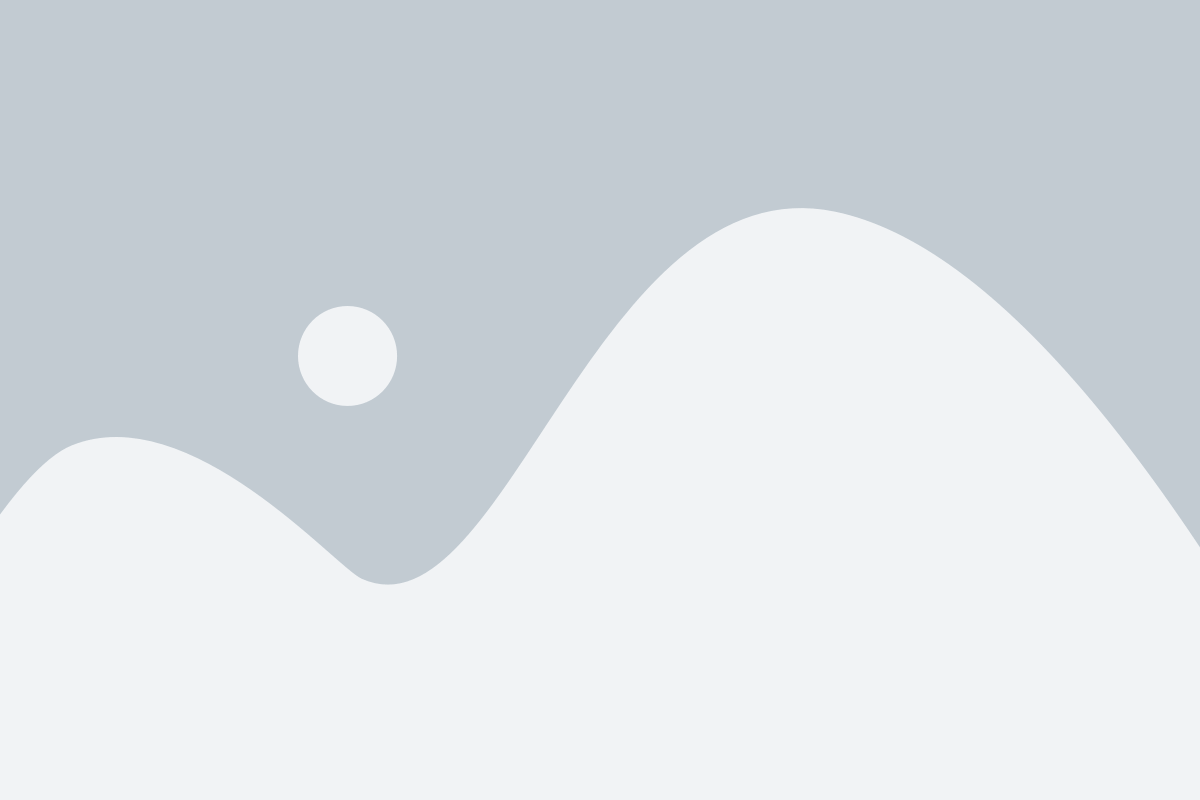
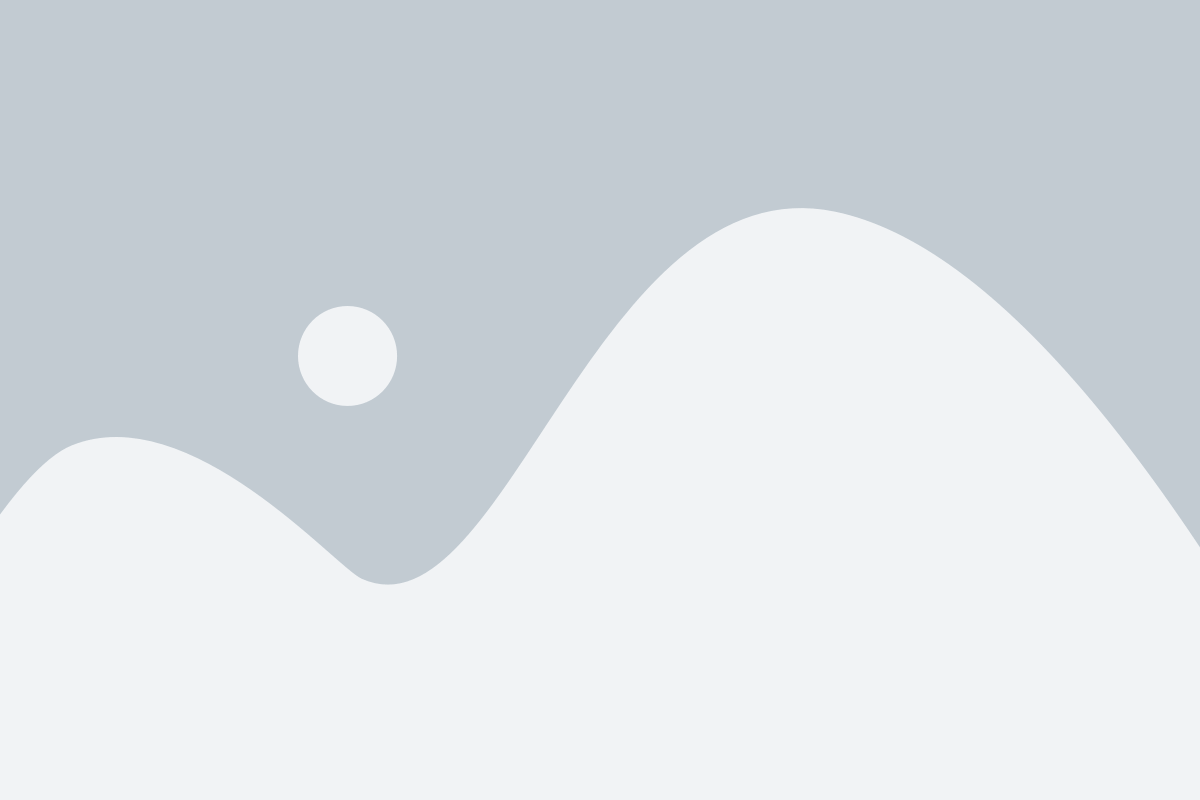
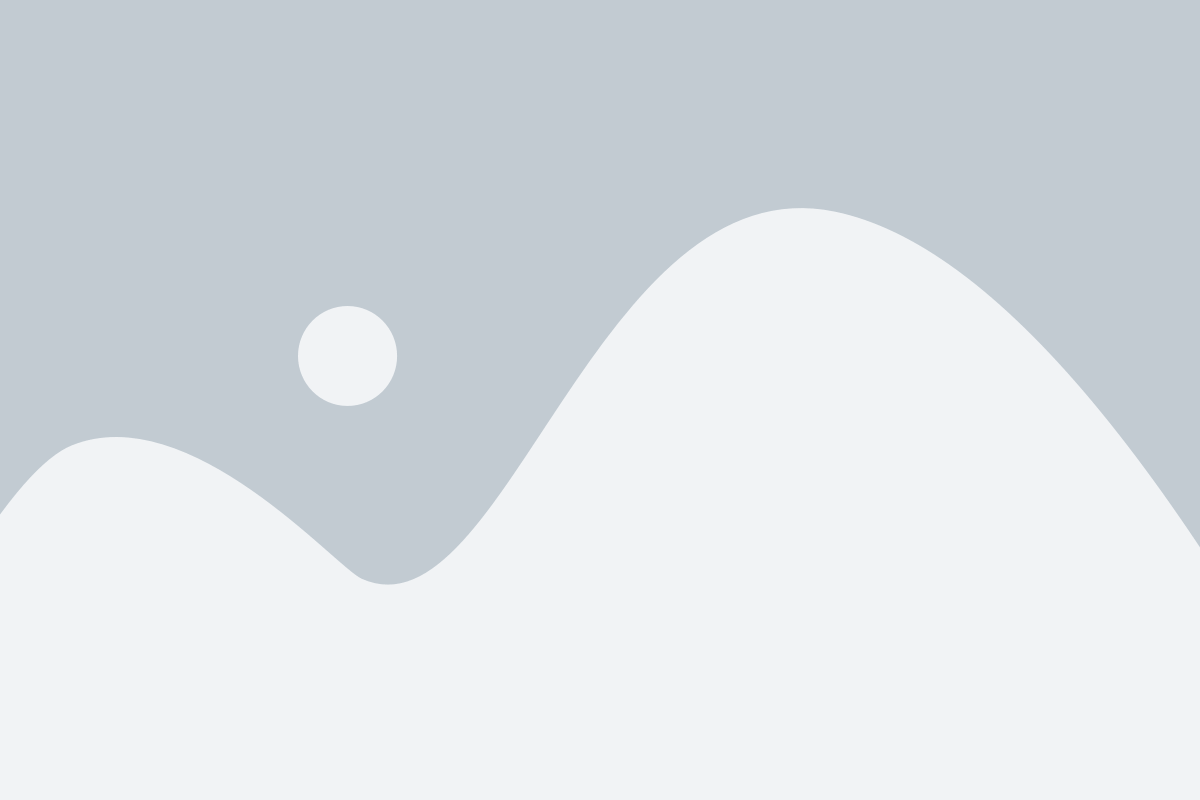
Coated Diamond Powder
The Comprehensive Guide
(2024)
Table of Contens
- 1. What is Coated Diamond Powder
- 2. Key Features and Benefits of Coatings
- 3. Coating Types and Their Functions
- 4.Available Grades, Grit Sizes, and Coating Thickness
- 5. Bond System Compatibility
- 6. Typical Applications in Various Industries
- 7. How to Select the Right Coated Diamond Powder
- 8.Sample Testing and Performance Verification
- 9.Packaging, Handling, and Storage Guidelines
What is Coated Diamond Powder?
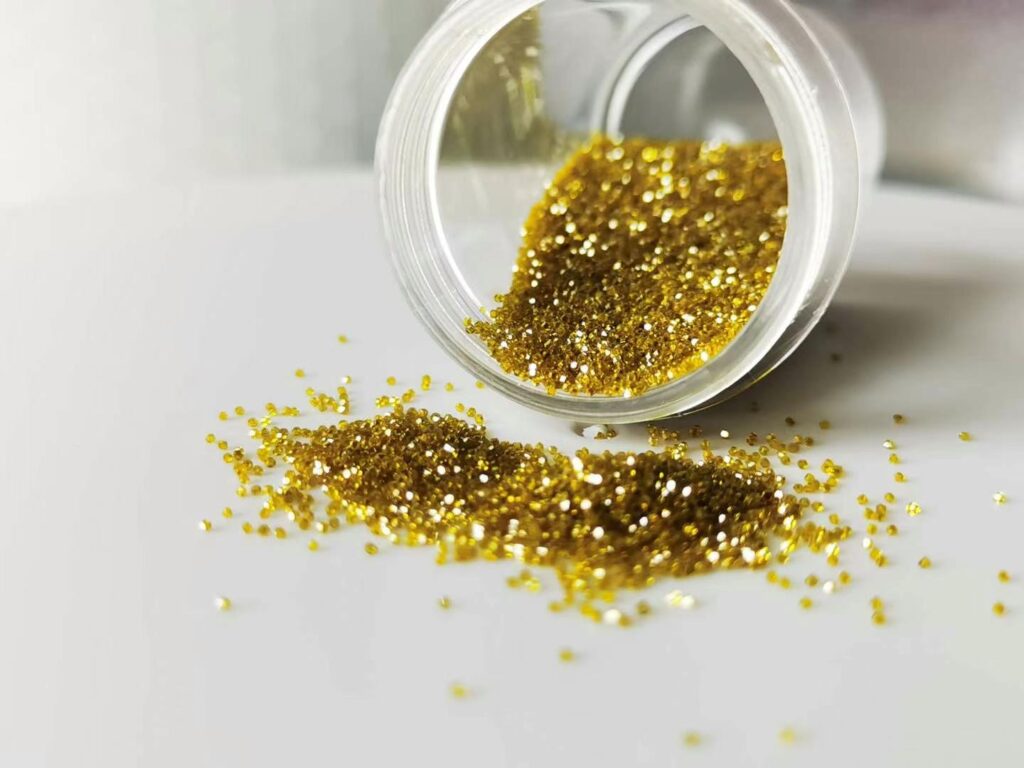
Key Features and Benefits of Coating Diamond
Enhanced Bond Retention
Improved Thermal Stability
Better Heat Dissipation
Consistent Coating Quality
Versatility Across Bond Systems
Coating Types and Their Functions
Available Grit Sizes, and Coating Thickness
Available Grit Sizes
Coating Thickness
Bond System Compatibility
Resin Bond
Vitrified Bond
Metal Bond (Sintered)
Electroplated Bond
Typical Applications in Various Industries
- Aerospace & Automotive:Grinding and cutting of tungsten carbide, ceramics, and high-silicon aluminium alloys for engine components, brakes, and structural parts.
- Electronics & Semiconductors:Precision lapping and polishing of optical glass, sapphire, and electronic substrates for displays, wafers, and sensors.
- Construction & Stone Processing:Cutting and shaping of granite, marble, and engineered stones in construction materials and decorative applications.
- Oil & Gas / Geology:Drilling and coring of hard rock and composites with high wear resistance and thermal stability tools for exploration equipment.
- Tool Manufacturing:Production of resin, metal, vitrified, and electroplated diamond tools for grinding, drilling, and cutting ultra-hard materials.
How to Select the Right Coated Diamond Powder
STEP 1
Match the Bond System
STEP 2
Choose the Appropriate Grit Size
STEP 3
Choose the Right Grit Size
STEP 4
Determine Coating Thickness
STEP 5
Consult Technical Experts
Quality Control and Consistency
Uniform Coating Quality: Advanced deposition techniques ensure an even and consistent coating layer on each particle, verified by SEM and thickness measurement, for reliable bond retention and thermal stability.
Precise Size and Shape Control: Every batch is graded with laser particle size analysers and precision sieving to achieve uniform particle size distribution and optimal crystal shape, ensuring predictable tool performance.
High Purity Standards: ICP and XRF testing are used to monitor and minimise impurities, preventing contamination and maintaining the integrity of your tools during high-temperature processing.
Consistent Batch Performance: All production lots are subject to magnetic separation, visual inspection, and sample testing to guarantee stable coating adhesion, particle quality, and performance from batch to batch.
Sample Testing and Performance Verification
Custom Sample Preparation
Application-Based Testing
Technical Support Service
Performance Feedback Loop
Packaging, Handling, and Storage Guidelines
- Moisture-proof and anti-static containers
- Sealed plastic bottles or vacuum-sealed foil bags
- Outer cartons for bulk protection
-
Custom packaging available on request
- Wear gloves and masks to avoid inhalation and skin contact
- Use clean, dry tools when opening or transferring
- Handle in a clean, controlled environment
- Keep sealed in original packaging until use
- Store in a cool, dry, and well-ventilated place
- Avoid moisture, sunlight, and extreme temperatures
An expert of agriculture protection textile specialist.
In the past 26 years, we’ve supported 100+ clients across 35 countries, including diamond tools manufacturers and synthetic diamond powder distributors to significantly enhance their product quality and efficiency. The purpose of article is to share insights on advanced abrasive solutions, helping you produce higher quality diamond tools with improved performance and durability.
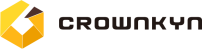
Precision Grinding & Polishing Solutions for Multiple Various Industrial Processing Fields
Company
Ask a Quote for Now
Requst a Free Quote
Send us a message if you have any questions or request a quote. We will be back to you ASAP.