Cubic Boron Nitiride Powder
Advanced CBN Powders for Your Precision Needs
Optimise Your Grinding and Cutting with Cubic Boron Nitride Powder
Cubic boron nitride (CBN) powder is indispensable in industries where exceptional hardness, thermal stability, and wear resistance are critical, such as precision grinding and cutting tool manufacturing. Crownkyn’s CBN powders excel with superior toughness and chemical stability, delivering reliable performance in demanding applications. Designed to meet specific industrial requirements, our powders enhance grinding efficiency and prolong tool life even under extreme conditions.
By partnering with Crownkyn, you secure a consistent source of quality and innovation. Our CBN powders are produced with tight control over particle size distribution and purity, ensuring they meet the highest industry expectations. Strengthen your manufacturing capabilities with Crownkyn’s advanced CBN powders — your dependable solution for performance, durability, and long-term value.
Improve efficiency with Crownkyn’s precision-engineered abrasive materials.
CBN Powder Manufacturer Serving Global Markets
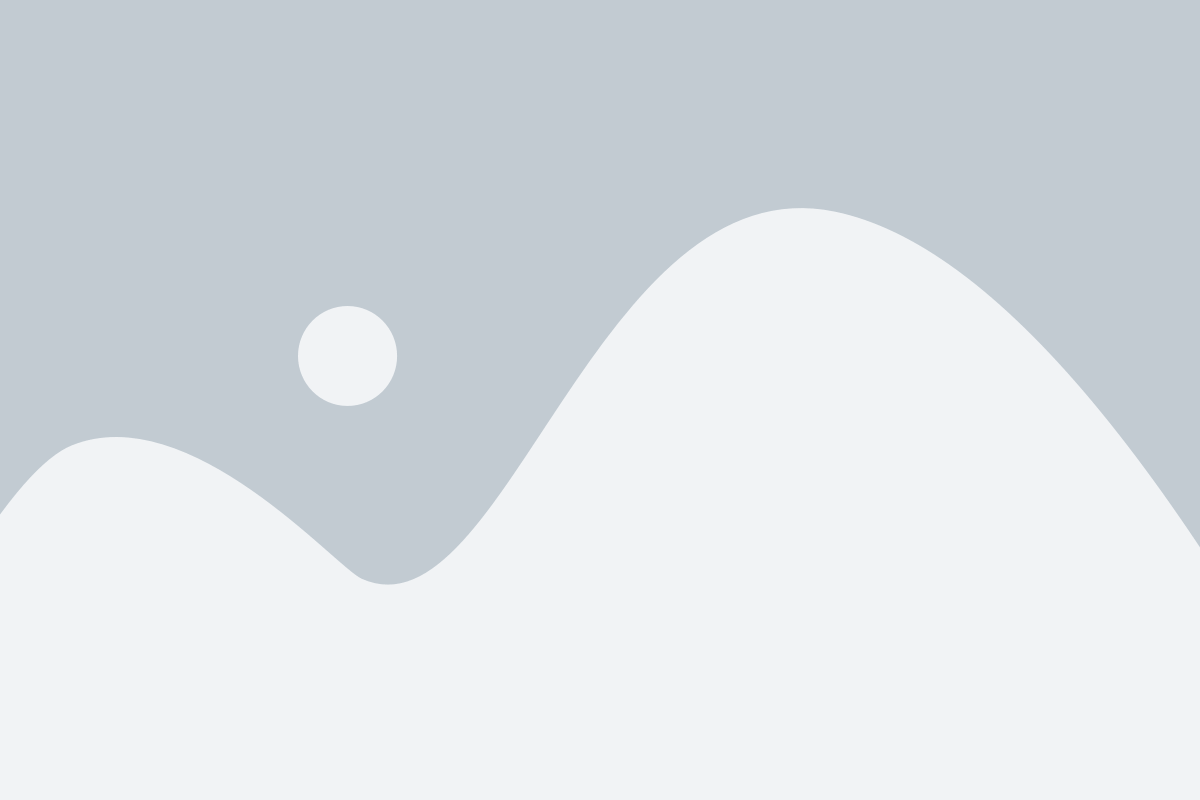
Custom CBN Powder Solutions To Your Needs
Product Grades Available: Choose from resin bond, metal bond, or vitrified bond CBN powders—each engineered to deliver optimal performance in demanding abrasive applications.
Application-Focused Solutions: Whether for precision grinding, surface finishing, or high-speed machining, our CBN powders are optimised to improve tool efficiency and durability.
Consistency & Precision: Count on stable quality and tightly controlled tolerances to ensure consistent results and reliable performance across every batch.
Advanced Coating Options: Optional surface coatings available to enhance bond adhesion, thermal stability, and overall abrasive efficiency.
Why Choose CBN Powder from Crownkyn Diamond
- Tailored to Your Needs: We understand that every grinding and finishing process is unique. That’s why we carefully define particle sizes and shapes to meet your specific requirements and ensure optimal results.
- Wide Range of Options: From fine powders for precision polishing to coarser grades for heavy-duty grinding, our diverse selection ensures you find the right solution for your application.
- Optimized Performance: With advanced production technology, we engineer CBN powders to deliver exceptional hardness, thermal stability, and cutting efficiency, helping you achieve consistent, high-quality finishes.
- Reliable Consistency: We maintain strict quality control to ensure uniform particle distribution and performance stability, supporting your processes with dependable and predictable results.
Frequently Asked Question
Manufacturing Workshop
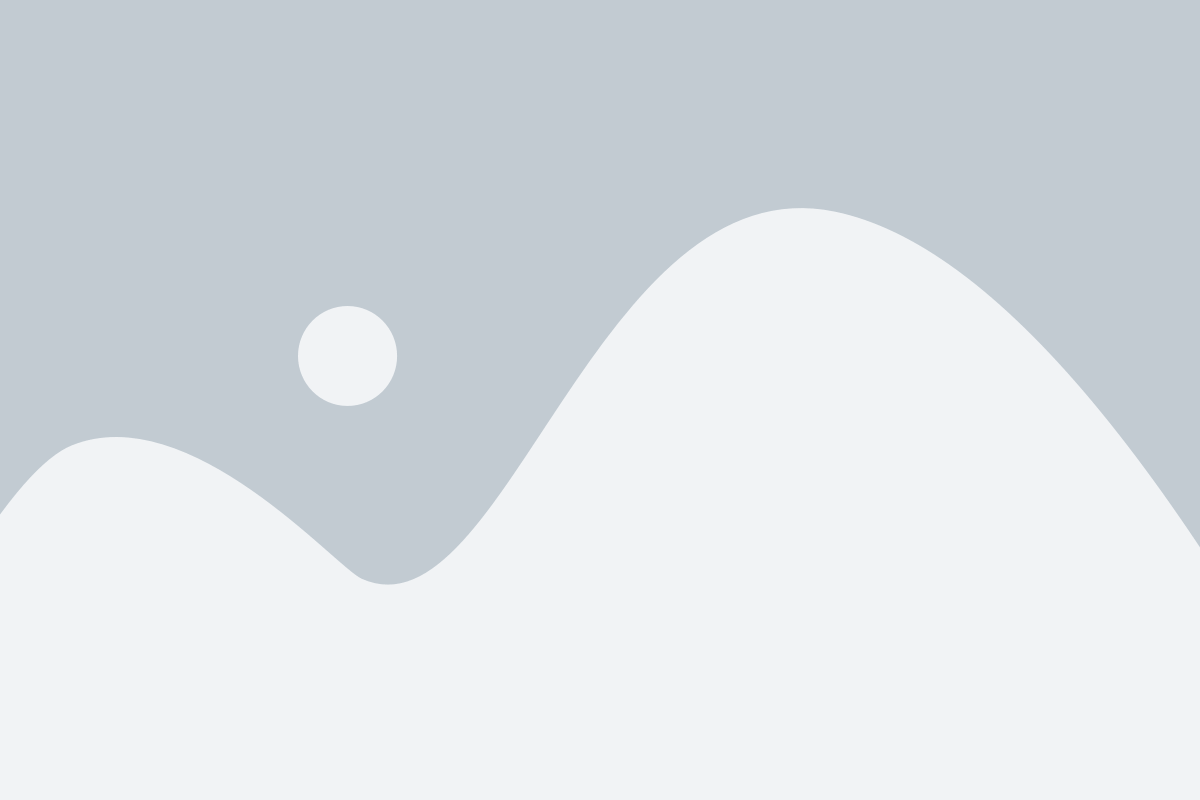
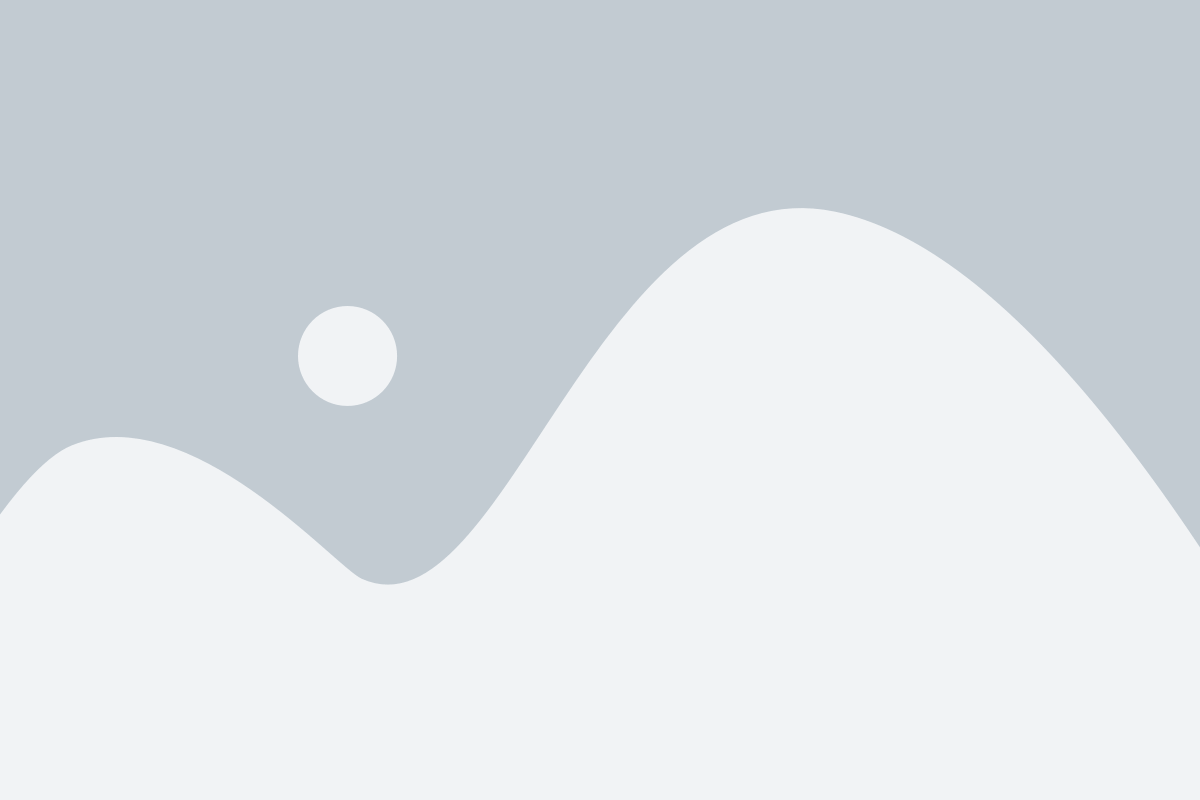
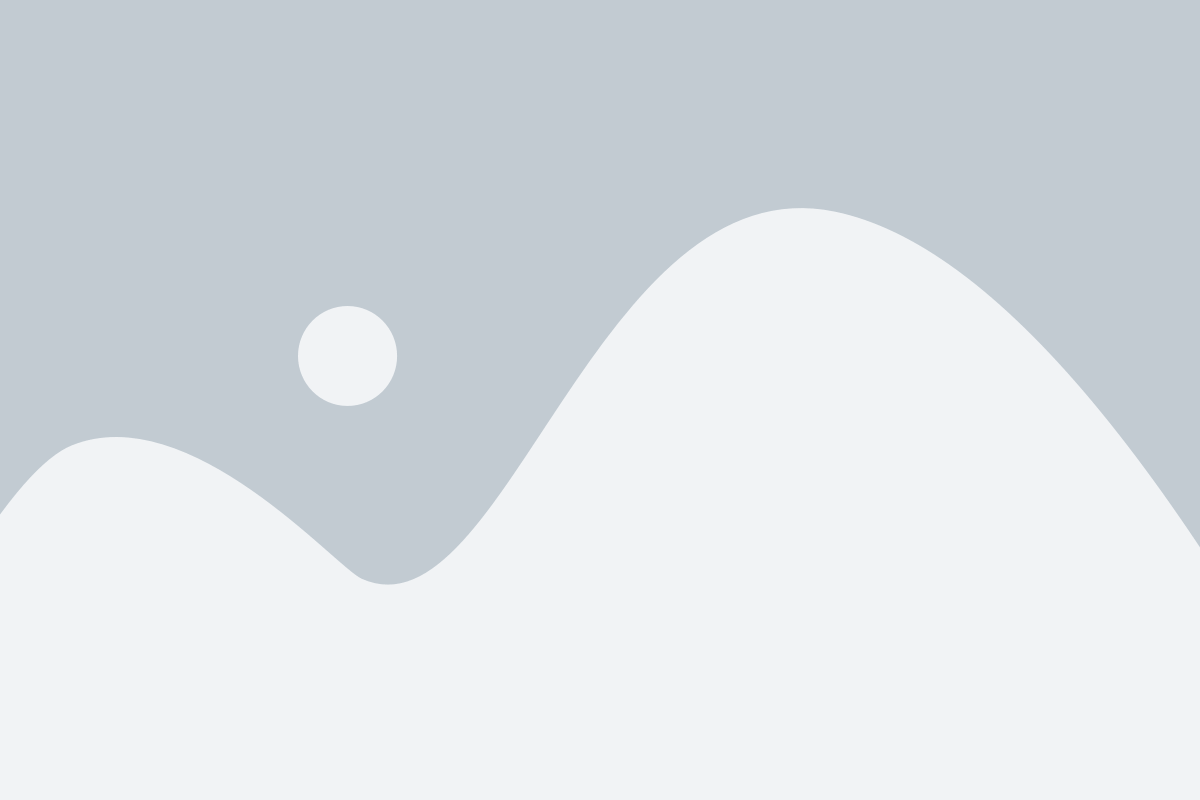
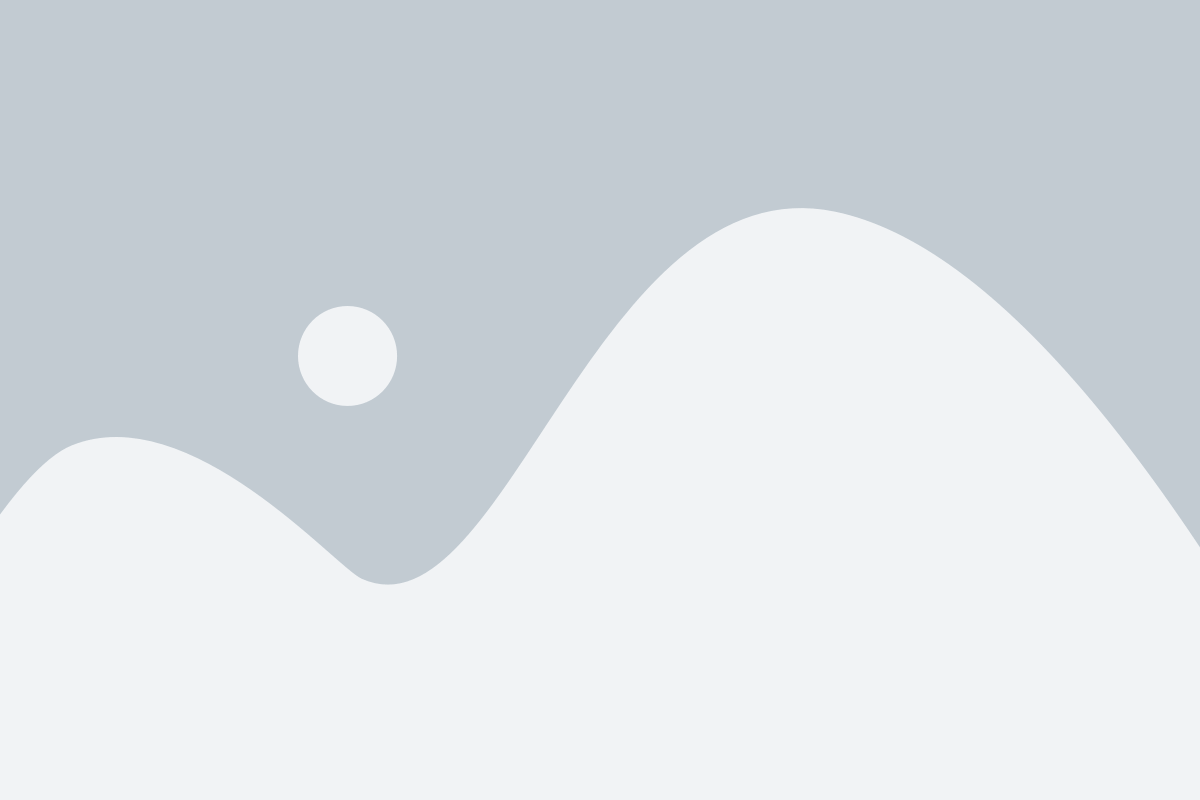
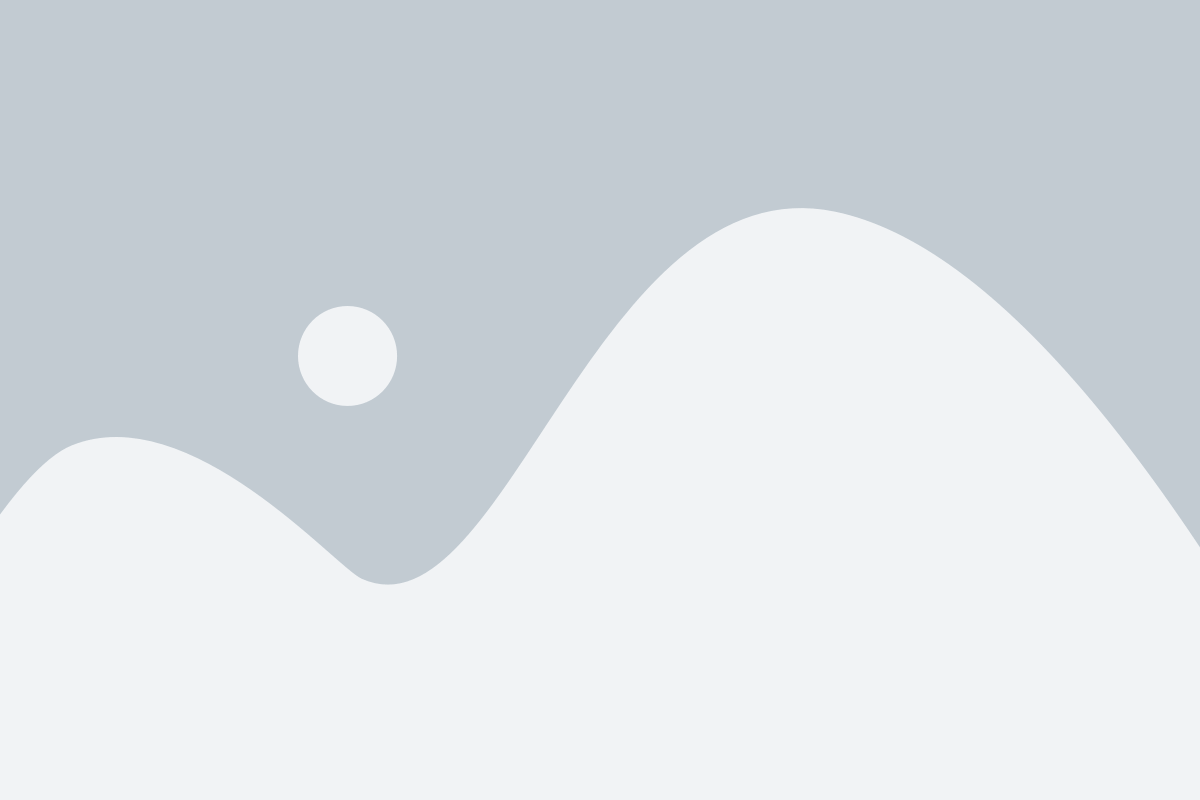
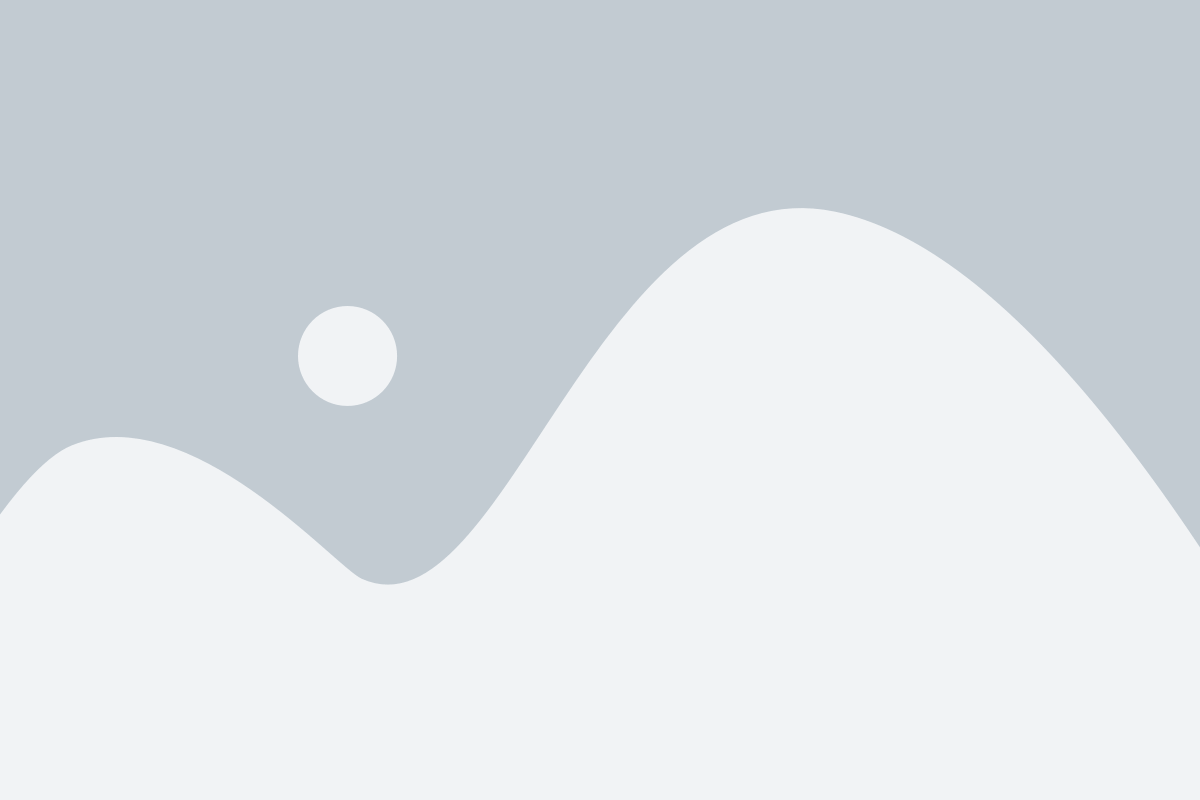
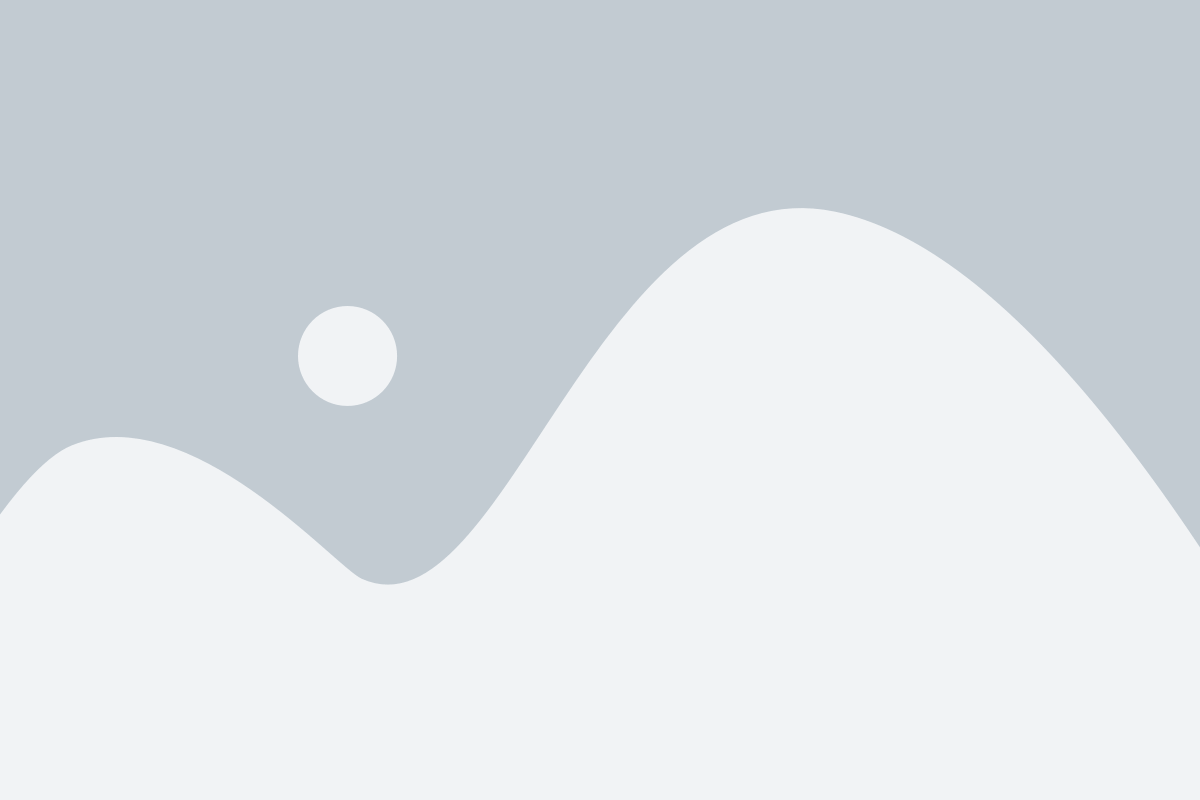
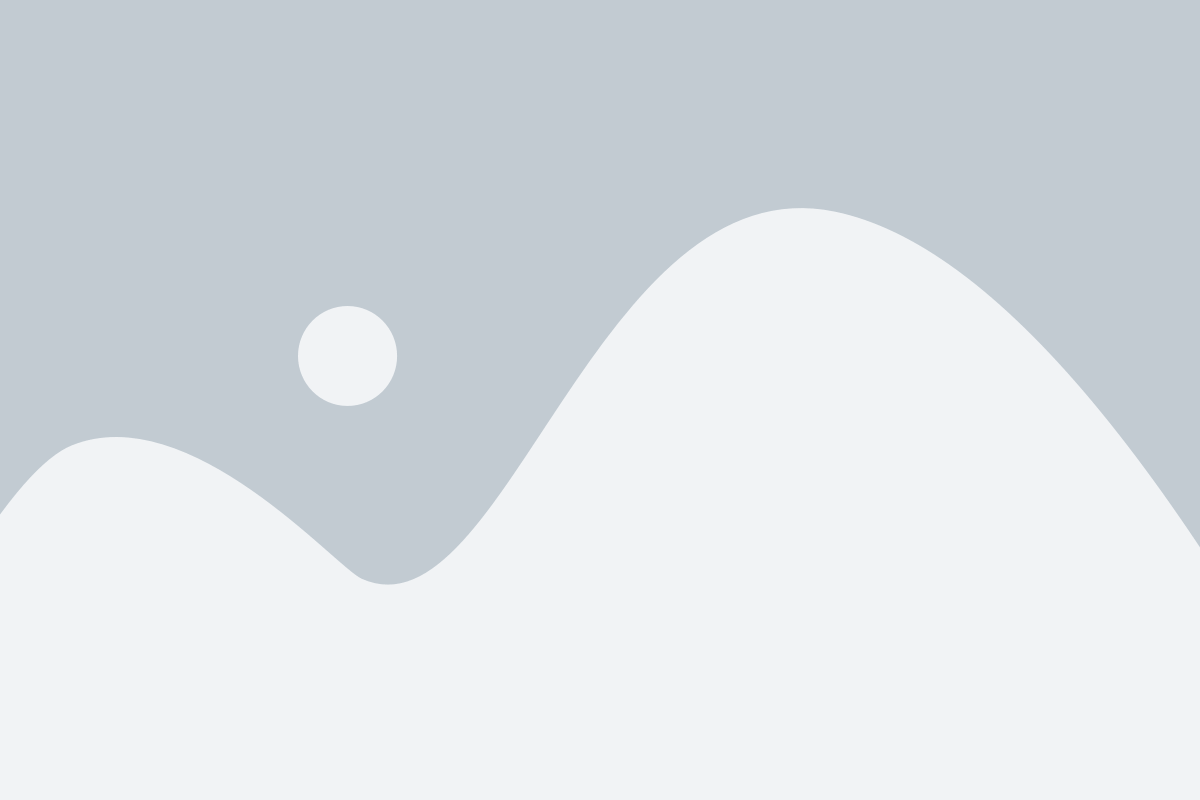
Cubic Boron Nitride (CBN) Powder
The Comprehensive Guide
(2024)
Table of Contens
- 1.What is Cubic Boron Nitride (CBN) Powder?
- 2. Key Properties and Advantages of CBN Powder
- 3. Available Grades, Particle Shapes, and Size Ranges
- 4. Bond System Compatibility
- 5.Typical Applications in Precision Grinding and Machining
- 6. Choose the Right CBN Powder for Your Process
- 7. Ensuring Consistency and Quality in Every Batch
- 8. Testing and Sample Assessment
- 9. Packaging, Handling, and Safe Storage Guidelines
What is Cubic Boron Nitride (CBN) Powder?
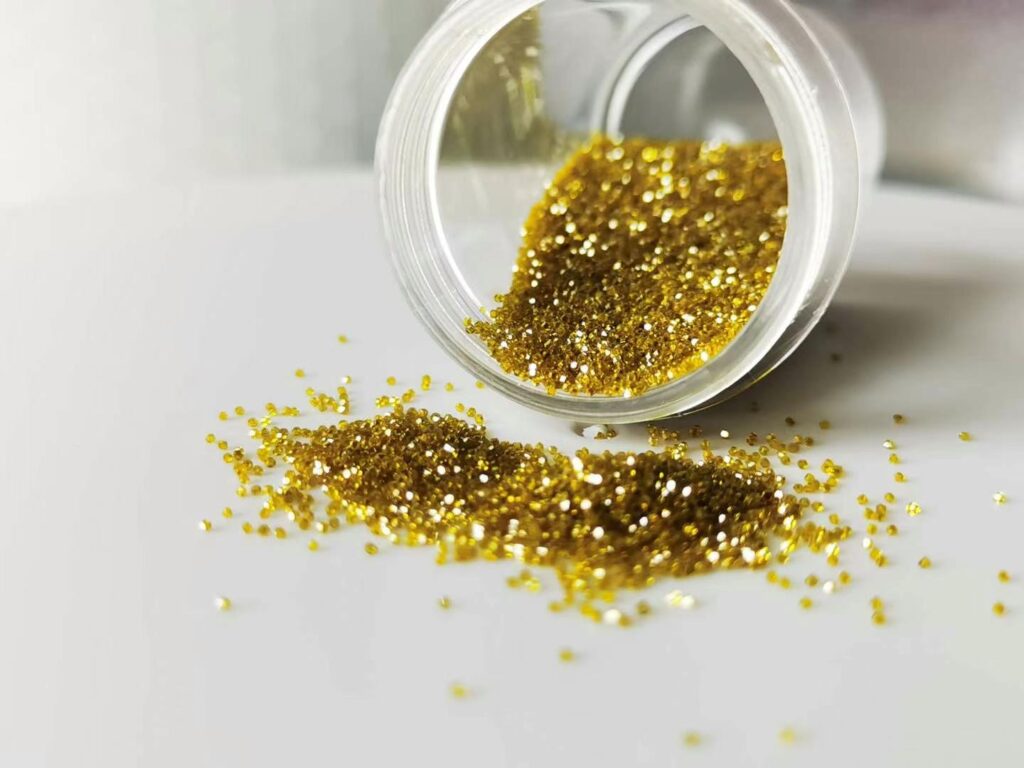
Key Properties and Advantages of CBN Powder
Sharp Multi-Angular Cutting Edges
High Thermal Stability
Excellent Bond Retention
Consistent Particle Size Distribution
Broad Application Versatility
Available Grades, Particle Shapes, and Size Ranges
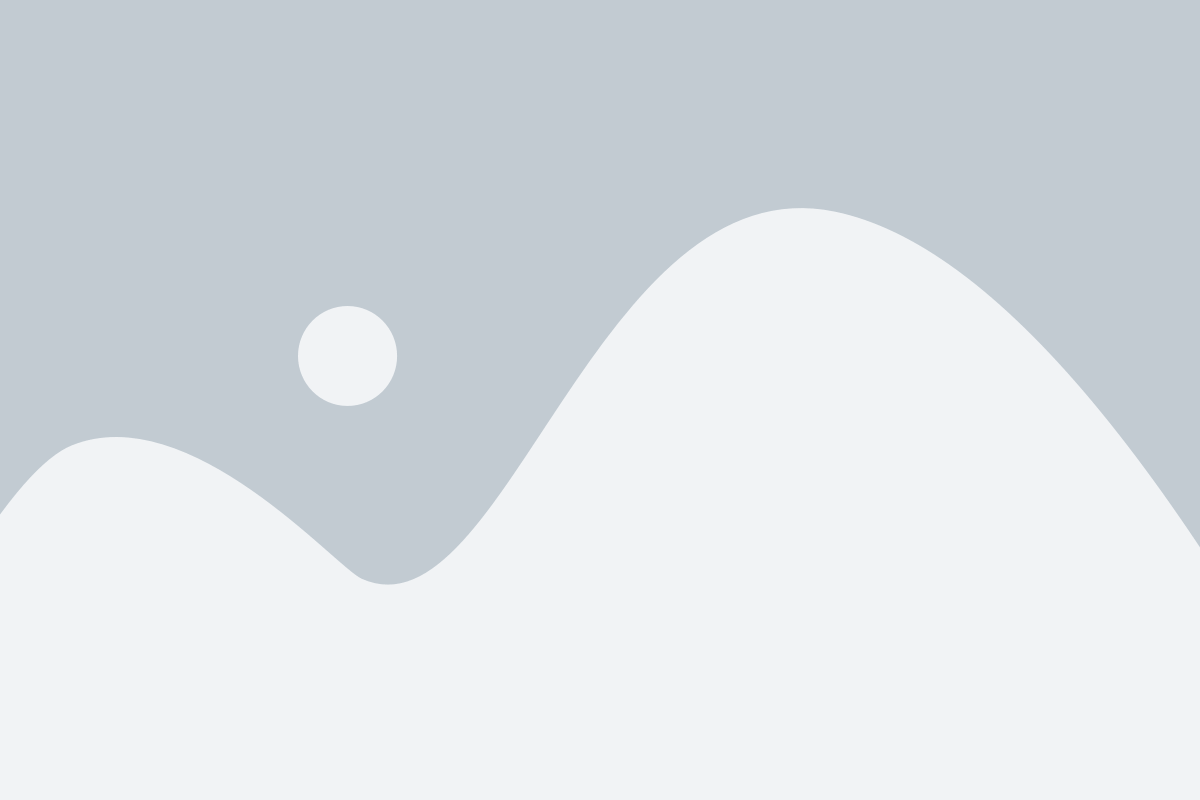
Standard Blocky CBN Powder
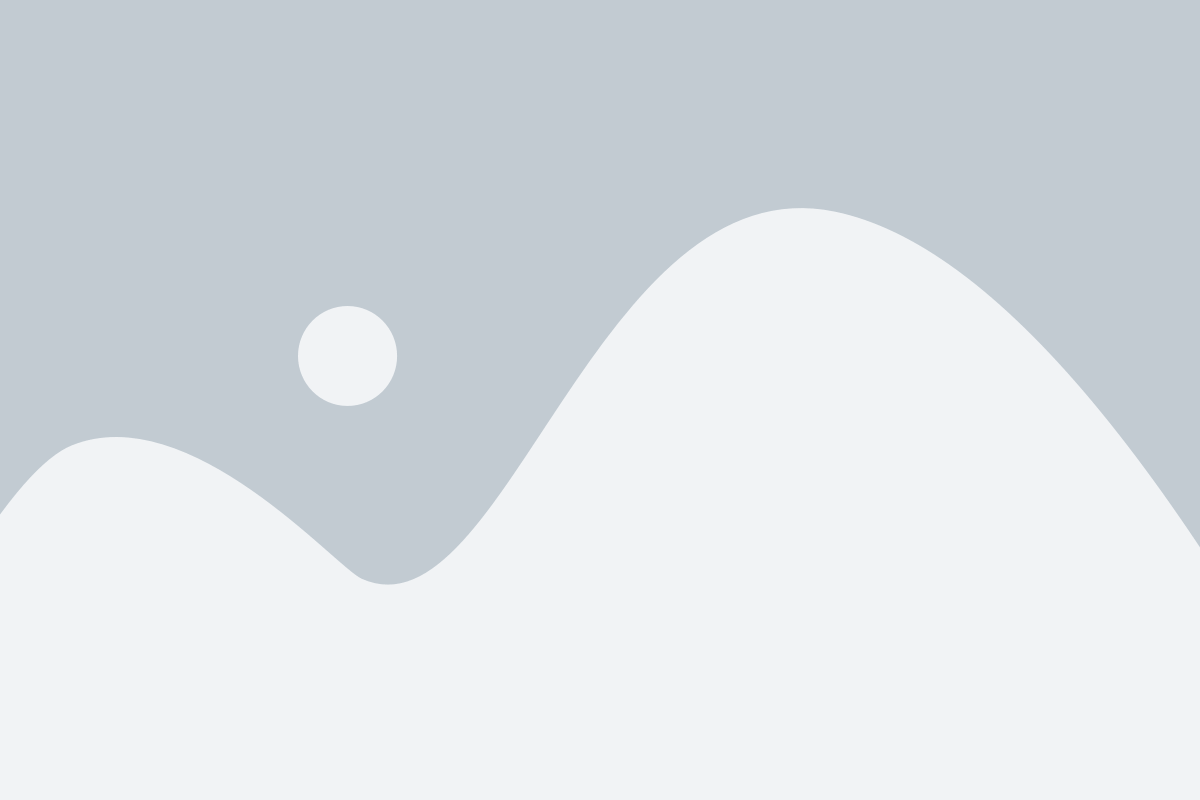
Shaped Blocky CBN Powder
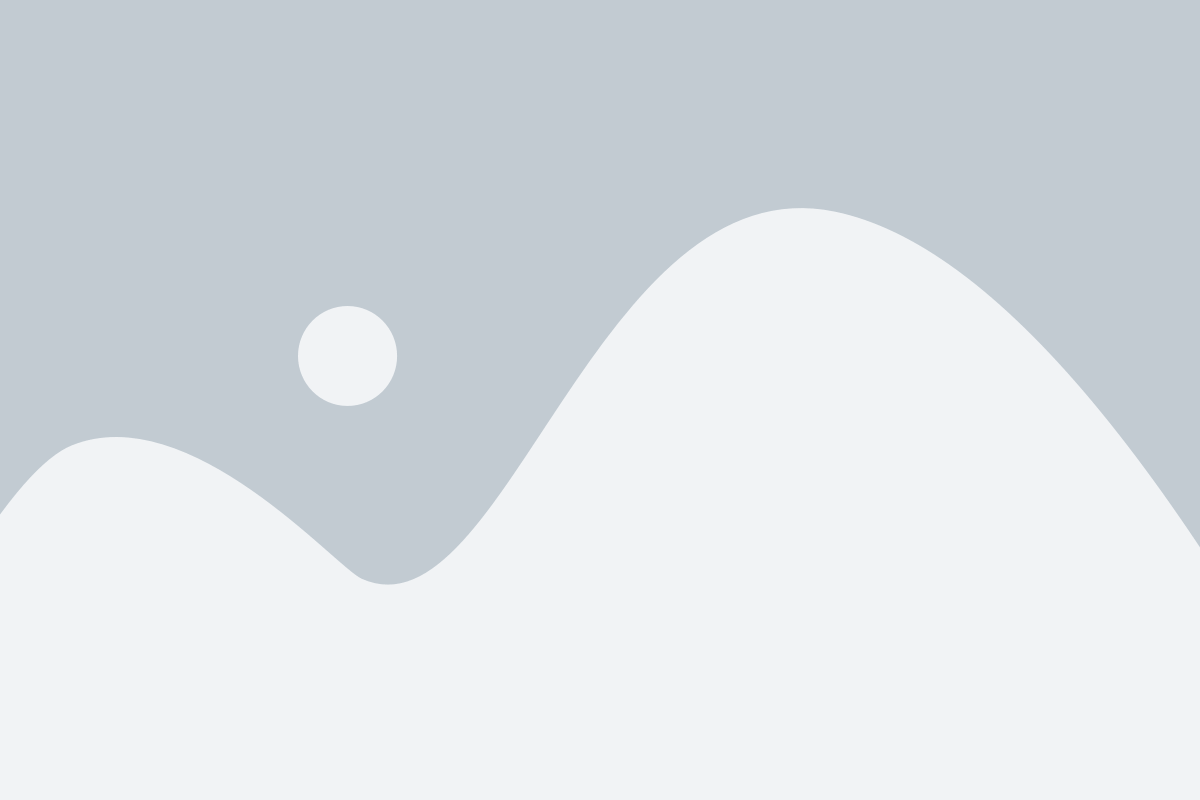
Coated CBN Powder
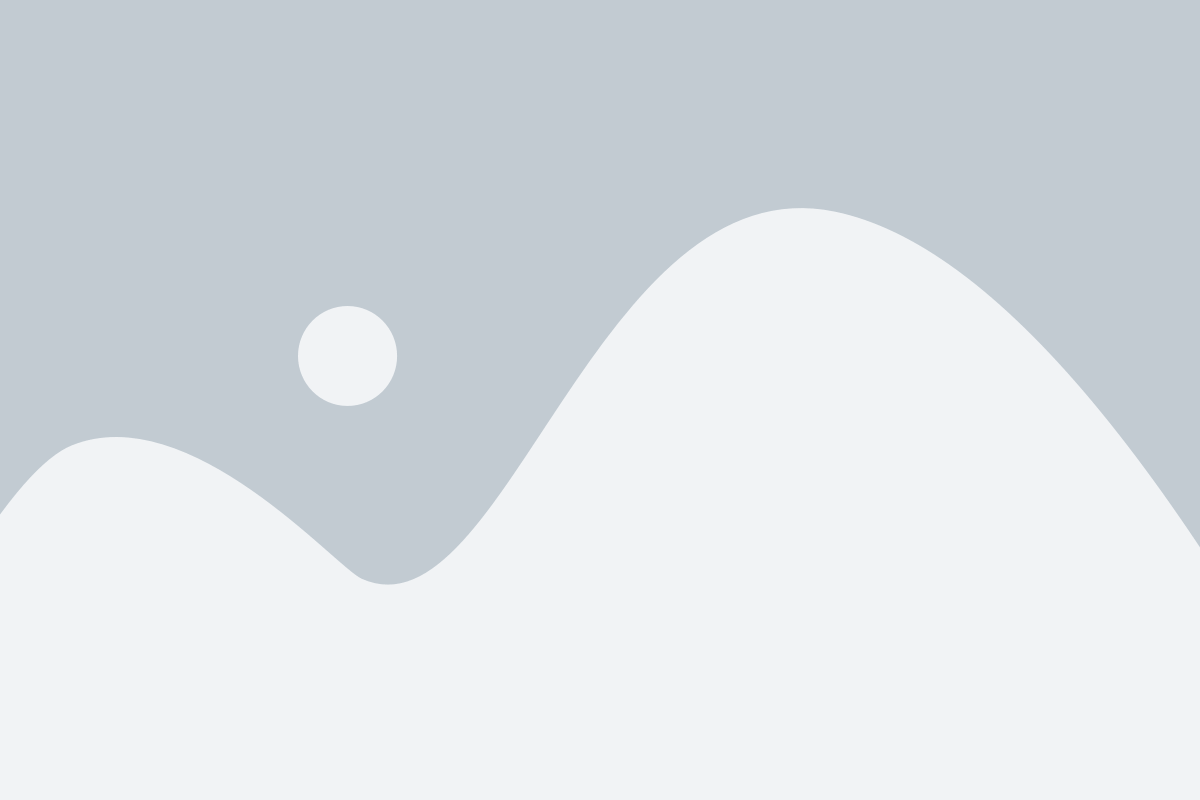
Micron and Submicron CBN Powder
Bond System Compatibility
Resin Bonds
Vitrified Bonds
CBN’s high thermal stability and uniform particle size make it well-suited for vitrified bond CBN tools, delivering consistent grinding performance and extended tool life under demanding conditions.
Metal Bonds
Electroplated Bonds
Typical Applications in Precision Grinding and Machining
Choose the Right CBN Powder for Your Process
STEP 1
Match the Bond System
STEP 2
Select the Appropriate Grade
STEP 3
Choose the Right Grit Size
STEP 4
Consider Particle Shape and Coating
STEP 5
Consult Technical Experts
Ensuring Consistency and Quality in Every Batch
Laser Particle Size Analyzer: Precisely measures particle size distribution, including D50, D90, and D10, ensuring uniformity and predictable grinding performance.
Scanning Electron Microscope (SEM): Examines crystal shape, surface structure, and morphology to verify sharpness, uniformity, and suitability for different bond systems.
X-Ray Diffraction (XRD): Confirms the cubic crystalline structure and purity of CBN, guaranteeing consistent material properties and hardness.
Toughness and Friability Testing: Assesses mechanical strength and resistance to fracture, helping select the right grade for specific grinding and machining applications.
Magnetic and Chemical Impurity Analysis: Detects and controls metallic and non-metallic impurities that can affect bond retention and grinding efficiency, especially in high-precision industries.
Thermal Stability Evaluation: Tests resistance to oxidation and thermal degradation under high temperatures, critical for metal bond and high-speed grinding tools.
Sample Testing and Technical Support
Custom Sample Preparation
Application-Oriented Testingg
Expert Technical Support
Continuous Improvement Feedback
Packaging, Handling, and Safe Storage Guidelines
- Moisture-proof, anti-static containers
- Sealed plastic jars or vacuum foil bags
- Strong cartons for bulk protection
- Custom packaging on request
- Wear gloves and mask to avoid contact or inhalation
- Use clean, dry tools for handling
- Work in a clean, controlled area
- Keep sealed in original container until needed
- Store in a cool, dry, ventilated environment
- Protect from moisture, direct sunlight, and high heat
An expert of agriculture protection textile specialist.
In the past 26 years, we’ve supported 100+ clients across 35 countries, including diamond tools manufacturers and synthetic diamond powder distributors to significantly enhance their product quality and efficiency. The purpose of article is to share insights on advanced abrasive solutions, helping you produce higher quality diamond tools with improved performance and durability.